Product Description
Matrix conductive sealants and adhesives are purpose-built for EMI shielding and environmental sealing in essential electronic applications. These electrically conductive formulations ensure effective EMI attenuation while forming robust seals that preserve IP ratings and environmental resistance. These products empower engineers to establish dependable, lasting bonds between components and enclosures. They find extensive utility in aerospace, telecommunications, automotive, and military sectors, delivering optimal electromagnetic interference protection in demanding environments.
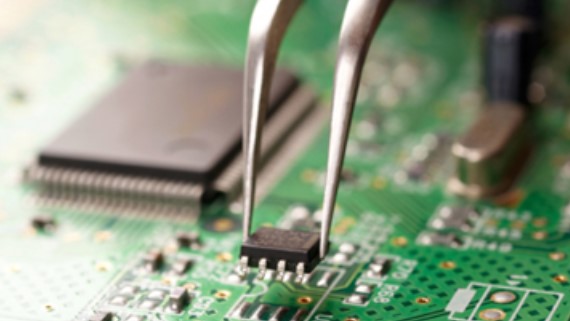
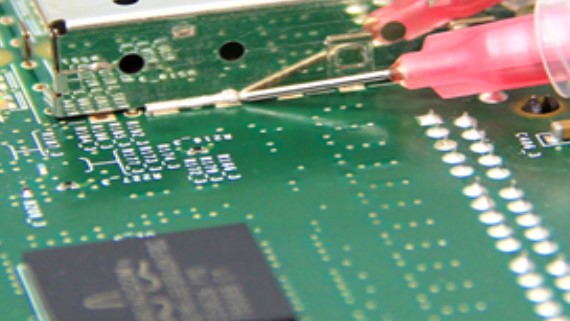
Value Added
In-house capabilities allow Matrix to control quality of customization, accommodate unique designs, and ensure compliance with stringent EMI shielding standards. This technical proficiency ensures cost-effective, high-performance solutions aligned with specific customer needs, making it a valuable proposition for engineers and industries seeking optimal EMI protection.
Frequently asked questions
If you have a question that is not addressed in our FAQ please click 'Contact Matrix' at the top of the page and submit. We will answer directly and add it to our FAQ to benefit the entire engineering community.
Your vision! Our expertise! Collaborating with engineering teams is what we do best! We listens to your priorities, and create a customized solution tailored to your specific requirements.
1. Conductive Silicone Sealants:
- Description: Silicone sealants infused with conductive additives.
- Benefit: High flexibility, exceptional environmental sealing, and robust EMI shielding, ideal for demanding electronics applications.
2. Electrically Conductive Epoxies:
- Description: Epoxies formulated with conductive particles.
- Benefit: Strong adhesion, outstanding EMI shielding performance, and enduring durability, perfect for aerospace and automotive component bonding.
3. Nickel-Filled Conductive Adhesives:
- Description: Adhesive compounds containing nickel-based conductive particles.
- Benefit: Superior electrical conductivity, excellent thermal stability, and reliable bonding for EMI-sensitive electronic components.
4. Silver-Filled Conductive Sealants:
- Description: Sealants enriched with silver-based conductive fillers.
- Benefit: Exceptional EMI shielding efficiency, outstanding thermal conductivity, and dependable sealing for RF enclosures.
5. Copper-Filled Conductive Adhesives:
- Description: Adhesive formulations featuring copper particles for conductivity.
- Benefit: High electrical conductivity, suited for bonding RF shields and electronic enclosures.
6. Graphene-Based Conductive Sealants:
- Description: Sealants incorporating graphene as a conductive material.
- Benefit: Enhanced electrical conductivity, lightweight properties, and applicability in advanced electronics and aerospace.
7. Water-Based Conductive Adhesives:
- Description: Adhesives with conductive materials dispersed in water.
- Benefit: Environmentally friendly, easy application, and compatibility with various substrates in electronics assembly processes.
8. Custom Formulations:
- Description: Tailored conductive sealants and adhesives to meet specific requirements.
- Benefit: Customized solutions for precise EMI shielding, bonding, and environmental sealing needs in specialized applications.
These conductive sealants and adhesive materials offer a wide array of electrical conductivity levels, environmental resistance capabilities, and adhesion strengths. They serve various industries, including aerospace, telecommunications, automotive, and military, where EMI shielding and component bonding are vital. Engineers can select the most suitable material based on their specific technical requirements.
Before selecting a conductive sealant or adhesive material, engineers should carefully evaluate several technical factors to ensure it aligns with their specific application requirements:
1. Electrical Conductivity: Assess the material’s electrical conductivity, measured in ohms per square (Ω/sq), ensuring it meets the desired EMI shielding and grounding needs.
2. Frequency Range: Determine the material’s effectiveness within the relevant frequency range to ensure optimal EMI attenuation.
3. Substrate Compatibility: Verify compatibility with the substrate material, considering factors like adhesion, thermal expansion coefficients, and potential chemical interactions.
4. Adhesion Properties: Evaluate the material’s adhesion strength to ensure a reliable and enduring bond between components and enclosures.
5. Environmental Resistance: Consider the material’s resistance to environmental factors such as temperature variations, humidity, and exposure to chemicals.
6. Ease of Application: Assess application methods, curing times, and handling procedures to ensure compatibility with the manufacturing process.
7. Customization: Determine the material’s ability to be customized for specific designs and bonding requirements.
8. Thermal Conductivity: Evaluate thermal conductivity, which can be crucial for dissipating heat in high-power electronic applications.
9. Mechanical Properties: Consider the material’s mechanical properties, including flexibility, hardness, and impact resistance, to ensure it can withstand mechanical stresses.
10. Regulatory Compliance: Ensure that the selected material complies with industry standards and regulations, such as RoHS (Restriction of Hazardous Substances) directives, if applicable.
11. Cost Considerations: Conduct a cost analysis, factoring in material costs, application method, and overall economic impact on the project.
12. Durability: Assess the material’s resistance to wear, tear, and long-term environmental exposure to ensure it maintains EMI shielding and bonding effectiveness over time.
13. Testing and Validation: Plan for EMI testing and validation to verify that the selected material meets the required shielding and bonding performance under real-world conditions.
By meticulously considering these technical factors, engineers can make informed decisions when selecting a conductive sealant or adhesive material that best suits their specific application’s requirements and ensures reliable EMI shielding and component bonding.
Conductive coatings and paints are frequently utilized in a variety of technical applications to address specific challenges related to electromagnetic interference (EMI) and electrical conductivity. Here are some high-technical examples of common applications:
1. Electronic Enclosures:
- Problem Solved: Protect sensitive electronic components from external EMI sources.
- Application: Coating the interior surfaces of electronic enclosures to form an EMI shield, ensuring the integrity of electronic systems.
2. Printed Circuit Boards (PCBs):
- Problem Solved: Prevent EMI emissions from PCBs that could interfere with nearby components.
- Application: Applying conductive coatings to PCBs to contain EMI and ensure signal integrity.
3. RF Enclosures:
- Problem Solved: Shield sensitive RF components from external interference.
- Application: Coating the interior surfaces of RF enclosures to prevent interference and maintain RF performance.
4. Antennas and Radar Systems:
- Problem Solved: Minimize signal loss and external EMI interference.
- Application: Coating antenna structures to enhance electrical conductivity, reduce signal loss, and maintain radar system performance.
5. Medical Devices:
- Problem Solved: Ensure the reliability and safety of medical equipment.
- Application: Applying conductive coatings to medical devices like MRI machines to prevent interference from external EMI sources.
6. Aerospace Electronics:
- Problem Solved: Protect avionics systems from external EMI threats.
- Application: Coating avionics equipment with conductive materials to maintain communication, navigation, and safety systems’ integrity.
7. Automotive Electronics:
- Problem Solved: Shield automotive control units from EMI sources.
- Application: Coating control units and communication systems in vehicles to prevent EMI interference.
8. Telecommunications Infrastructure:
- Problem Solved: Ensure uninterrupted data transmission in telecom equipment.
- Application: Coating telecom infrastructure components like base stations and signal processing units to protect against external EMI sources.
9. Industrial Automation:
- Problem Solved: Safeguard control panels and equipment from EMI.
- Application: Coating control panels and automation equipment to ensure smooth manufacturing processes and prevent EMI-related disruptions.
10. Consumer Electronics:
- Problem Solved: Enhance the performance and reliability of consumer devices.
- Application: Applying conductive coatings to consumer electronics components to reduce interference and maintain product functionality.
Conductive coatings and paints play a vital role in these applications by addressing EMI-related challenges, safeguarding electronic systems, and maintaining reliable performance in various industries.
COMPARE
Compare Options
Click below to get a customized comparison chart tailored to your application.
1
2
3
1 | 2 | 3 | |
Consideration | Nickel-Based Sealant | Graphite-Based Sealant | Water-Based Sealant |
Electrical Conductivity | Very Good | Good | Moderate |
Frequency Range | Very Good | Good | Moderate |
Substrate Compatibility | Very Good | Good | Good |
Adhesion Strength | Good | Very Good | Good |
Environmental Resistance | Very Good | Good | Good |
Ease of Application | Good | Good | Very Good |
Customization | Good | Good | Good |
Thermal Conductivity | Very Good | Good | Moderate |
Mechanical Properties | Good | Very Good | Good |
Cost | Moderate | Moderate | Good |