Product Description
Matrix Conductive Heat Spreaders, which include thermal gap fillers, graphite-based, and aluminum-based options, are advanced solutions designed to efficiently dissipate heat in electronic applications. Conductive heat spreaders, also known as heat spread materials, are essential components that help distribute and transfer heat away from electronic components and devices, ensuring they operate within safe temperature ranges and maintaining optimal performance and reliability. Engineers across industries, such as aerospace, automotive, telecommunications, and data centers, rely on Matrix heat spreaders to address thermal management challenges effectively.
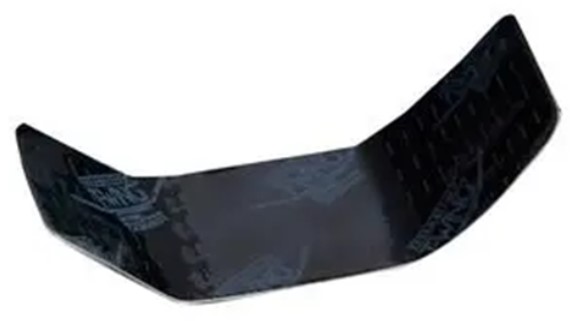
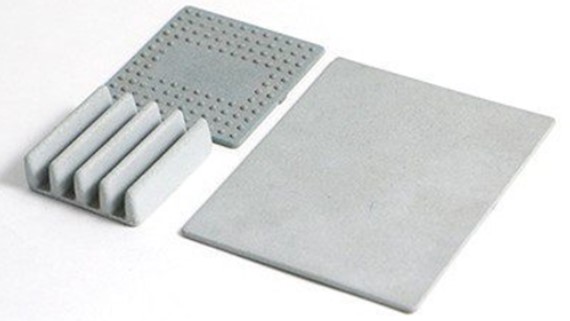
Value Added
Matrix offers added value to our conductive heat spreading materials by offering tailored solutions made in-house. We leverage our expertise in material selection, custom cutting, and application knowledge to optimize material performance for specific customer requirements. We also provide rapid prototyping, supply chain management, and just-in-time delivery, ensuring that you receive customized heat spreading solutions that meet your exact specifications, improve thermal management, and enhance the reliability of your electronic systems
Frequently asked questions
If you have a question that is not addressed in our FAQ please click 'Contact Matrix' at the top of the page and submit. We will answer directly and add it to our FAQ to benefit the entire engineering community.
Your vision! Our expertise! Collaborating with engineering teams is what we do best! We listens to your priorities, and create a customized solution tailored to your specific requirements.
1. Thermal Gap Fillers:
- Description: These elastomeric materials fill gaps between components to enhance thermal conductivity.
- Benefits: Excellent conformability, low thermal resistance, and reliable heat transfer for efficient thermal management.
2. Graphite-Based Heat Spreaders:
- Description: These spreaders use graphite for high thermal conductivity and lightweight properties.
- Benefits: Exceptional thermal conductivity, reduced weight, and improved heat dissipation for enhanced performance.
3. Aluminum-Based Heat Spreaders:
- Description: Aluminum-based spreaders provide good thermal conductivity with flexibility.
- Benefits: Efficient heat transfer, flexibility for conforming to irregular surfaces, and improved thermal management.
4. Graphite Thermal Pads:
- Description: These pads use graphite and a polymer matrix for efficient heat transfer.
- Benefits: High thermal conductivity, electrical insulation, and ease of use in various applications.
5. Phase Change Materials (PCMs):
- Description: PCMs change phase at specific temperatures to provide efficient heat spreading.
- Benefits: Precise temperature control, improved thermal performance, and reduced thermal resistance.
6. Metal Foil-Based Heat Spreaders:
- Description: Metal foil spreaders use materials like copper or aluminum for efficient heat spreading.
- Benefits: High thermal conductivity, durability, and effective heat dissipation for demanding applications.
7. Synthetic Graphite Films:
- Description: Synthetic graphite films offer high thermal conductivity in thin, flexible sheets.
- Benefits: Thin profile, excellent thermal performance, and adaptability for space-constrained applications.
8. Ceramic-Based Heat Spreaders:
- Description: Ceramic-based spreaders provide excellent thermal conductivity and electrical insulation.
- Benefits: High thermal performance, electrical insulation, and suitability for diverse applications.
Each of these conductive heat spreading materials from Matrix serves specific engineering needs, offering tailored solutions for diverse electronic and thermal management applications.
1. Thermal Conductivity (k):
- Evaluate the material’s thermal conductivity, which determines how efficiently it can transfer heat. Higher thermal conductivity is often preferred for better heat dissipation.
2. Thickness and Gap Filling:
- Determine the material’s thickness and its ability to fill gaps between components. Proper gap filling is essential for uniform heat transfer.
3. Thermal Resistance (R):
- Calculate the thermal resistance of the material, considering the thickness, thermal conductivity, and interface conditions. Lower thermal resistance results in better heat spreading.
4. Electrical Conductivity:
- Ensure the material’s electrical conductivity is compatible with the application requirements. Some applications require electrical insulation to prevent short circuits.
5. Compressibility and Conformability:
- Assess the material’s ability to conform to irregular surfaces and components. Adequate compressibility is crucial for maintaining good thermal contact.
6. Operating Temperature Range:
- Verify that the material can withstand the operating temperature range of the application without degradation or phase change.
7. Chemical Compatibility:
- Consider the material’s resistance to chemicals, moisture, and environmental factors in the application’s operating environment.
8. Durability and Longevity:
- Evaluate the material’s durability over time, including resistance to mechanical stress, wear, and tear.
9. Application Method:
- Choose a material that suits the intended application method, whether it’s pre-cut sheets, dispensed compounds, or other forms.
10. Cost Analysis:
- Factor in material costs and processing expenses to align with budget constraints.
11. Customization Options:
- Determine if the material can be customized to specific shapes, sizes, or formulations to meet unique application requirements.
12. Regulatory Compliance:
- Ensure that the selected material meets industry-specific standards and regulations, such as RoHS and UL listings.
By meticulously considering these technical factors, engineers can select the most suitable conductive heat spreading material to address thermal management challenges effectively in their specific applications.
Conductive heat spreaders find common use in various industries and applications to solve specific technical challenges. Here are some examples, along with the problems they address:
1. Microelectronics and Semiconductors:
- Problem: Miniaturized electronic components generate heat concentration, risking thermal stress and performance degradation.
- Solution: Conductive heat spreaders efficiently dissipate heat, ensuring consistent component operation.
- Industries: Electronics manufacturing, microelectronics.
2. Aerospace and Avionics:
- Problem: Aerospace systems encounter extreme temperature variations and must maintain reliable performance.
- Solution: Heat spreaders manage temperature fluctuations, preventing component overheating and ensuring mission-critical functionality.
- Industries: Aerospace, avionics.
3. Automotive Electronics:
- Problem: Automotive electronics require protection against thermal stress and environmental factors.
- Solution: Conductive heat spreaders maintain optimal operating temperatures, preventing overheating-related failures.
- Industries: Automotive, electric vehicles (EVs).
4. LED Lighting:
- Problem: High-power LEDs generate heat that can affect efficiency and lifespan.
- Solution: Heat spreaders dissipate heat, enhancing LED efficiency and prolonging their operational life.
- Industries: Lighting, architectural lighting.
5. Telecommunications:
- Problem: Telecom equipment faces temperature fluctuations and environmental exposure.
- Solution: Heat spreaders ensure reliable operation in diverse weather conditions, preventing overheating and signal degradation.
- Industries: Telecommunications, network infrastructure.
6. Renewable Energy Systems:
- Problem: Solar inverters and wind turbines require heat management for efficient energy conversion.
- Solution: Heat spreaders help maintain optimal operating temperatures, improving energy conversion efficiency.
- Industries: Renewable energy, solar power, wind energy.
7. Data Centers:
- Problem: Data centers generate significant heat, impacting server reliability and energy efficiency.
- Solution: Heat spreaders manage thermal loads, enhancing cooling efficiency and reducing energy consumption.
- Industries: Data centers, information technology.
8. Medical Devices:
- Problem: Medical equipment needs protection from thermal stress and sterilization processes.
- Solution: Conductive heat spreaders safeguard electronics, ensuring reliable and sterile device performance.
- Industries: Healthcare, medical device manufacturing.
9. Industrial Automation:
- Problem: Industrial control systems operate in harsh environments with temperature fluctuations.
- Solution: Heat spreaders maintain consistent temperatures, enhancing the reliability of automation systems.
- Industries: Manufacturing, industrial automation.
10. Consumer Electronics:
- Problem: Mobile devices and laptops require heat management to prevent overheating and component damage.
- Solution: Heat spreaders maintain safe operating temperatures, improving device longevity and performance.
- Industries: Consumer electronics.
Conductive heat spreaders play a crucial role in these technical applications and industries by effectively addressing thermal management challenges and ensuring the reliable operation of electronic systems and components.
COMPARE
Compare Options
Click below chart to get a customized chart specific to your application.
1
2
3
1 | 2 | 3 | |
Consideration | Thermal Gap Fillers |
Graphite-Based Spreaders |
Aluminum-Based Spreaders |
Thermal Conductivity (k) | Good | Very Good | Good |
Thickness and Gap Filling Capability | Very Good | Moderate | Moderate |
Thermal Resistance (R) | Moderate | Good | Moderate |
Electrical Insulation | Moderate | Very Good | Good |
Compressibility and Conformability | Very Good | Moderate | Moderate |
Operating Temperature Range | Good | Very Good | Good |
Chemical Compatibility | Good | Good | Good |
Durability and Longevity | Good | Good | Good |
Customization Options | Good | Good | Good |
Cost Analysis | Good | Good | Good |