Product Description
Matrix rugged and harsh environment cable assembly solutions excel in challenging conditions, featuring robust construction, resistance to moisture, chemicals, and temperature extremes. Engineers benefit from enhanced reliability, durability, and signal integrity, ideal for industries like aerospace, oil and gas, and automotive manufacturing. These cable assemblies adhere to stringent standards, ensuring uninterrupted performance in mission-critical applications, while offering customization options to suit diverse engineering needs, facilitating efficient connectivity and durability in extreme environments.
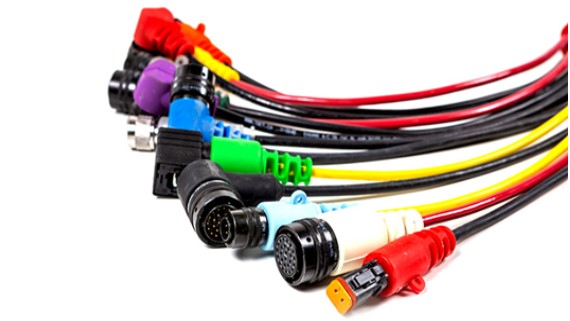
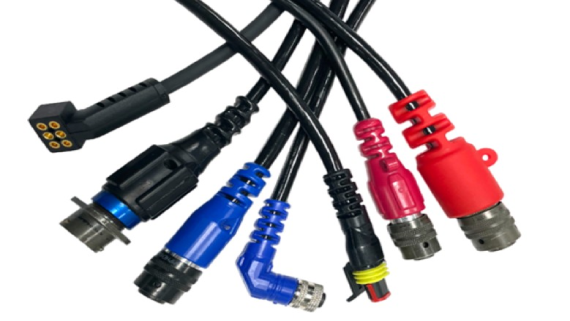
Value Added
Matrix engineers rugged cable assemblies with meticulous attention to detail, utilizing advanced materials like UV-resistant jackets and precision overmolding for environmental resilience. Employing techniques such as potting and strain relief, Matrix ensures optimal strain resistance and electrical performance. Engineers benefit from durable, customized solutions that withstand harsh conditions, reducing downtime and maintenance efforts, while maintaining consistent signal integrity in demanding applications
Frequently asked questions
If you have a question that is not addressed in our FAQ please click 'Contact Matrix' at the top of the page and submit. We will answer directly and add it to our FAQ to benefit the entire engineering community.
Your vision! Our expertise! Collaborating with engineering teams is what we do best! We listens to your priorities, and create a customized solution tailored to your specific requirements.
1. High-Temperature Cable Assemblies:
- Description: Designed for extreme heat environments.
- Primary Benefit for Engineers: Maintains signal integrity and reliability in high-temperature industrial processes and equipment.
2. Oil and Chemical Resistant Cable Assemblies:
- Description: Resistant to oil, chemicals, and solvents.
- Primary Benefit for Engineers: Ensures cable integrity and longevity in oil and chemical processing plants.
3. Waterproof and Submersible Cable Assemblies:
- Description: Sealed against water and submersion.
- Primary Benefit for Engineers: Ideal for marine, underwater, and outdoor applications, safeguarding against moisture and corrosion.
4. EMI/RFI Shielded Cable Assemblies:
- Description: Provides electromagnetic and radiofrequency interference protection.
- Primary Benefit for Engineers: Maintains signal quality and prevents interference in sensitive electronics and data transmission.
5. Abrasion-Resistant Cable Assemblies:
- Description: Withstands physical abrasion and wear.
- Primary Benefit for Engineers: Enhances cable longevity in rugged industrial machinery and harsh environments.
6. Vibration-Resistant Cable Assemblies:
- Description: Designed to withstand vibrations.
- Primary Benefit for Engineers: Ensures stable electrical connections in machinery exposed to vibrations, reducing downtime.
7. Fire-Resistant Cable Assemblies:
- Description: Resistant to flames and high temperatures.
- Primary Benefit for Engineers: Provides fire protection for critical applications like aerospace and rail systems.
8. Solar and UV-Resistant Cable Assemblies:
- Description: UV-stable materials for outdoor solar installations.
- Primary Benefit for Engineers: Maintains cable integrity in solar panels, even in direct sunlight.
9. Shock-Resistant Cable Assemblies:
- Description: Withstands mechanical shocks and impacts.
- Primary Benefit for Engineers: Ensures cable reliability in applications prone to physical shocks, like automotive and military.
10. Customized Specialty Cable Assemblies:
- Description: Tailored to specific project requirements.
- Primary Benefit for Engineers: Offers flexibility to meet unique application needs, optimizing cable performance and durability.
1. Environmental Conditions:
- Evaluate the operating environment, including temperature extremes, humidity, exposure to chemicals, UV radiation, water, and dust.
2. Material Selection:
- Choose materials that can withstand environmental factors and are resistant to chemicals, abrasion, and UV exposure.
3. Cable Jacket and Insulation:
- Select ruggedized cable jackets and insulation materials suitable for the environment and temperature range.
4. Connectors and Terminations:
- Use connectors and terminations designed for harsh environments, ensuring secure connections and protection against moisture and dust ingress.
5. Strain Relief and Cable Entry:
- Implement strain relief mechanisms to prevent cable damage due to bending, twisting, or pulling.
- Ensure proper cable entry seals to prevent environmental contaminants from entering the assembly.
6. Shielding:
- Include appropriate shielding to protect against electromagnetic interference (EMI) and radiofrequency interference (RFI).
7. Connector Sealing and Gaskets:
- Use sealing materials and gaskets to create a watertight and dustproof seal at connector interfaces.
8. Vibration and Shock Resistance:
- Design cable assemblies to withstand vibrations and mechanical shocks encountered in rugged applications.
9. Flex Life and Bend Radius:
- Ensure cable assemblies can endure repeated flexing and bending without damage.
10. Compliance with Standards:
- Verify that the design complies with industry-specific standards and regulations for ruggedized cable assemblies.
11. Testing and Quality Control:
- Implement rigorous testing protocols, including environmental testing (e.g., temperature cycling, vibration testing) to validate performance under harsh conditions.
12. Customization:
- Tailor the cable assembly to meet specific application requirements, including cable length, connectors, and breakout options.
13. Serviceability and Repair ability
- Design the assembly to allow for ease of maintenance and repair in the field, reducing downtime.
14. Cost Optimization
- Balance ruggedization measures with cost considerations, ensuring a cost-effective solution without compromising performance.
15. Cable Routing and Management:
- Plan cable routing within the equipment or system to minimize exposure to environmental hazards.
16. IP Ratings:
- Consider IP (Ingress Protection) ratings to ensure the assembly’s resistance to dust and water intrusion.
17. Chemical Compatibility:
- Assess the compatibility of cable materials with any chemicals present in the environment.
1. Aerospace and Defense:
- Problem: Extreme temperatures, vibrations, and electromagnetic interference in aircraft and military equipment.
- Solution: Ruggedized cable assemblies withstand harsh conditions, ensuring reliable data and power connections.
- Industry/Application: Avionics, military vehicles, communication systems.
2. Oil and Gas Exploration:
- Problem: Corrosive chemicals, abrasion, and extreme weather in drilling and extraction operations.
- Solution: Ruggedized cables resist chemicals and protect against mechanical wear and environmental factors.
- Industry/Application: Drilling equipment, offshore platforms.
3. Automotive Manufacturing:
- Problem: Robotic automation and welding environments subject cables to mechanical stress and high temperatures.
- Solution: Ruggedized cable assemblies withstand heat and offer strain relief, enhancing automation reliability.
- Industry/Application: Automotive assembly lines, welding robots.
4. Mining and Mineral Processing:
- Problem: Abrasion, dust, and vibrations in mining equipment.
- Solution: Specialty ruggedized cables endure harsh mining conditions, reducing maintenance.
- Industry/Application: Mining machinery, mineral extraction.
5. Marine and Offshore Applications:
- Problem: Saltwater, moisture, and UV exposure in marine environments.
- Solution: Waterproof and UV-resistant cable assemblies safeguard against corrosion and weather.
- Industry/Application: Shipboard systems, offshore platforms.
6. Railway and Transportation Systems:
- Problem: Vibrations, temperature fluctuations, and exposure to elements.
- Solution: Ruggedized cables ensure reliable connections in railway signaling, communication, and control systems.
- Industry/Application: Rail transportation, signaling systems.
7. Renewable Energy Systems:
- Problem: Outdoor exposure, temperature variations, and UV radiation in solar and wind installations.
- Solution: Solar- and UV-resistant cable assemblies maintain performance in renewable energy systems.
- Industry/Application: Solar farms, wind turbines.
8. Industrial Automation and Robotics:
- Problem: Extreme temperatures, mechanical stress, and vibrations in automated machinery.
- Solution: Ruggedized cables enhance cable longevity and ensure reliable automation.
- Industry/Application: Manufacturing automation, robotics.
9. Outdoor Telecommunications Infrastructure:
- Problem: Exposure to weather, moisture, and temperature fluctuations.
- Solution: Waterproof and weather-resistant cable assemblies protect outdoor telecom infrastructure.
- Industry/Application: Telecom towers, outdoor networking.
10. Harsh Laboratory Environments:
- Problem: Chemical exposure, temperature fluctuations, and mechanical stress.
- Solution: Chemical-resistant and high-temperature cables endure lab conditions.
- Industry/Application: Scientific research, laboratory equipment.
COMPARE
Compare Options
Click below to get a customized comparison chart tailored to your application.
1
2
3
1 | 2 | 3 | |
Consideration | Harsh & Rugged Cable Assembly A |
Harsh & Rugged Cable Assembly B |
Harsh & Rugged Cable Assembly C |
Environmental Resistance | Very Good | Good | Very Good |
Material Durability | Very Good | Very Good | Good |
Connector and Termination | Very Good | Very Good | Good |
EMI/RFI Shielding | Very Good | Good | Very Good |
Temperature Range | Very Good | Good | Very Good |
Vibration and Shock Resistance | Very Good | Good | Good |
Chemical Resistance | Good | Good | Very Good |
IP Rating | Very Good | Good | Very Good |
Customization Options | Good | Very Good | Moderate |
Cost-Efficiency | Moderate | Good | Moderate |