Product Description
Matrix Phase Change Thermal Interface Materials (TIMs) are advanced solutions designed for precise thermal management in electronics. With high thermal conductivity and phase change properties, these TIMs ensure efficient heat transfer, reducing thermal resistance for superior thermal performance. They find extensive use in critical industries like telecommunications, automotive electronics, and aerospace, where maintaining optimal operating temperatures is essential.
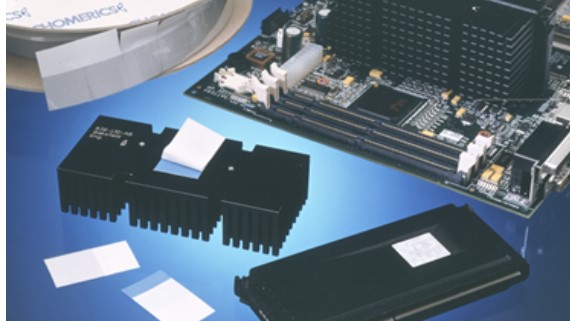
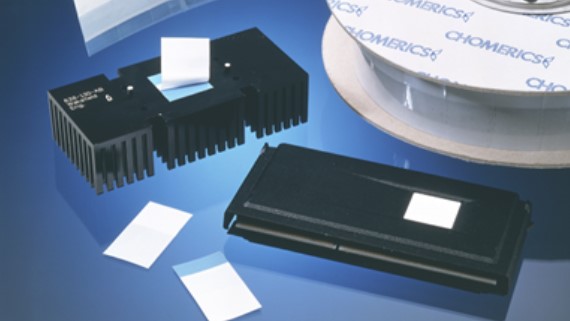
Value Added
Matrix adds value to phase change materials (PCMs) in-house by customizing PCM solutions to meet specific customer needs. This involves cutting PCMs to precise shapes and sizes required for individual applications, optimizing thermal performance. Our expertise in matching PCM properties to unique customer requirements ensures optimal thermal management solutions. Furthermore, we provide technical support, rapid prototyping, and just-in-time delivery, offering a comprehensive solution package that enhances the effectiveness and efficiency of your PCM applications.
Frequently asked questions
If you have a question that is not addressed in our FAQ please click 'Contact Matrix' at the top of the page and submit. We will answer directly and add it to our FAQ to benefit the entire engineering community.
Your vision! Our expertise! Collaborating with engineering teams is what we do best! We listens to your priorities, and create a customized solution tailored to your specific requirements.
1. Paraffin-Based Phase Change Materials:
- Description: Matrix paraffin-based PCMs are engineered with specific paraffin compounds that exhibit phase transitions at precise temperature thresholds, providing predictable thermal control.
- Benefits: These PCMs offer exceptional heat absorption and release capabilities, making them ideal for applications requiring precise temperature regulation, such as semiconductor cooling.
2. Non-Paraffin-Based Phase Change Materials:
- Description: Matrix non-paraffin-based PCMs leverage alternative materials to achieve tailored phase change behavior, ensuring precise temperature management in diverse environments.
- Benefits: Non-paraffin-based PCMs allow customization of phase change properties, enhancing their suitability for applications demanding strict thermal control, like aerospace electronics.
3. Customized Phase Change Materials:
- Description: Matrix offers customization options, allowing engineers to tailor PCM formulations to meet unique thermal management requirements, including phase transition temperatures and specific heat capacities.
- Benefits: Custom PCMs empower engineers to fine-tune thermal solutions, optimizing heat transfer efficiency in applications such as medical devices with stringent temperature constraints.
Selecting the right phase change material (PCM) for a thermal management application requires careful consideration of several technical factors:
1. Phase Change Temperature (Tc):
- Consideration: Determine the specific temperature range at which the PCM transitions between solid and liquid phases.
- Importance: Matching Tc to the application’s operating temperature is crucial for optimal thermal performance.
2. Latent Heat of Fusion (ΔH):
- Consideration: Evaluate the amount of energy absorbed or released during the phase change.
- Importance: Higher ΔH values indicate greater heat absorption/release capacity, which can impact the PCM’s effectiveness.
3. Thermal Conductivity (k):
- Consideration: Assess the material’s ability to conduct heat during both solid and liquid phases.
- Importance: High thermal conductivity enhances heat transfer efficiency.
4. Thermal Resistance (R):
- Consideration: Calculate the thermal resistance of the PCM to understand its impact on heat transfer.
- Importance: Lower thermal resistance minimizes temperature gradients, improving thermal control.
5. Cycle Life:
- Consideration: Determine how many thermal cycles the PCM can endure without performance degradation.
- Importance: Long cycle life is critical for applications with repeated temperature fluctuations.
6. Volume Change:
- Consideration: Analyze whether the PCM undergoes significant volume changes during phase transitions.
- Importance: Volume stability is crucial in applications with space constraints or sensitive components.
7. Chemical Compatibility:
- Consideration: Verify the PCM’s compatibility with surrounding materials and potential chemical interactions.
- Importance: Incompatibility can lead to material degradation or adverse effects on system components.
8. Thermal Stability:
- Consideration: Assess the PCM’s ability to withstand temperature extremes without degradation.
- Importance: Thermal stability is critical for long-term reliability.
9. Environmental Impact:
- Consideration: Consider the PCM’s environmental impact, including toxicity and recyclability.
- Importance: Environmentally friendly options align with sustainability goals.
10. Application-Specific Requirements:
- Consideration: Account for any unique requirements, such as size, shape, or phase change kinetics.
- Importance: Tailoring the PCM to meet application-specific demands can optimize performance.
11. Regulatory Compliance:
- Consideration: Ensure that the selected PCM complies with industry standards and regulations, such as RoHS (Restriction of Hazardous Substances) for electronics.
12. Cost:
- Consideration: Evaluate the cost-effectiveness of the PCM, including material and handling expenses.
- Importance: Cost considerations should align with performance and application requirements.
By meticulously considering these technical factors, engineers can make informed decisions when selecting a phase change material, ensuring it meets the precise thermal management needs of their application.
Phase change materials (PCMs) find common and valuable applications across various industries due to their ability to address specific thermal management challenges. Here are some technical examples of industries and the problems PCMs solve:
1. Electronics Cooling (e.g., Data Centers):
- Problem: Heat generated by electronic components can lead to temperature spikes and reduced performance.
- Solution: PCMs absorb excess heat during peak loads and release it during off-peak periods, maintaining stable temperatures.
- Industry: Data centers, telecommunications, high-performance computing.
2. Aerospace and Avionics:
- Problem: Temperature variations during flight can affect sensitive avionics equipment.
- Solution: PCMs stabilize temperatures, preventing overheating and ensuring reliable performance.
- Industry: Aerospace, avionics, satellite systems.
3. Automotive Thermal Management:
- Problem: Electric vehicle batteries require precise temperature control for optimal efficiency and longevity.
- Solution: PCMs assist in maintaining battery temperature within the desired range, improving battery life and performance.
- Industry: Electric vehicle manufacturing, automotive.
4. Building Energy Efficiency:
- Problem: Fluctuating external temperatures challenge HVAC systems.
- Solution: PCMs integrated into building materials absorb heat during the day and release it at night, reducing HVAC energy consumption.
- Industry: Construction, green building design.
5. Medical Devices:
- Problem: Medical equipment generates heat that can affect patient comfort and device performance.
- Solution: PCMs manage heat, ensuring the safe operation of medical devices and patient comfort.
- Industry: Healthcare, medical device manufacturing.
6. Consumer Electronics:
- Problem: Portable devices can experience thermal throttling due to heat buildup.
- Solution: PCMs prevent overheating, allowing devices to maintain consistent performance.
- Industry: Consumer electronics, smartphones, laptops.
7. Solar Energy Storage:
- Problem: Solar energy storage systems need temperature control to maintain efficiency.
- Solution: PCMs help regulate temperatures, improving energy storage and conversion efficiency.
- Industry: Renewable energy, solar power systems.
8. Textile Industry:
- Problem: Clothing for extreme conditions must balance warmth and breathability.
- Solution: PCM-infused textiles regulate body temperature by absorbing and releasing heat.
- Industry: Apparel manufacturing, outdoor gear.
9. Food and Beverage:
- Problem: Maintaining precise temperatures during transportation and storage is crucial for food safety.
- Solution: PCMs act as thermal barriers, preventing temperature fluctuations.
- Industry: Food logistics, cold chain management.
10. Thermal Energy Storage:
- Problem: Efficient storage and utilization of thermal energy are essential for renewable energy systems.
- Solution: PCMs store excess thermal energy during peak production for later use, improving energy system efficiency.
- Industry: Renewable energy, energy storage.
These technical examples illustrate how PCMs address diverse thermal challenges across industries, ensuring reliable operation, energy efficiency, and enhanced performance in a wide range of applications.
COMPARE
Compare Options
Click below chart to get a customized chart specific to your application.
1
2
3
1 | 2 | 3 | |
Consideration | Manufacturer A | Manufacturer B | Manufacturer C |
Phase Change Temperature (Tc) | Very Good | Good | Excellent |
Latent Heat of Fusion (ΔH) | Good | Very Good | Excellent |
Thermal Conductivity (k) | Moderate | Good | Very Good |
Thermal Resistance (R) | Moderate | Good | Very Good |
Cycle Life | Moderate | Very Good | Excellent |
Volume Change | Moderate | Good | Very Good |
Chemical Compatibility | Moderate | Good | Very Good |
Thermal Stability | Moderate | Good | Very Good |
Environmental Impact | Moderate | Good | Very Good |
Cost | Moderate | Good | Very Good |