Product Description
Matrix Cure-In-Place Potting Materials offer engineers versatile solutions for encapsulating and safeguarding electronic components. These materials, available in epoxy, silicone, and urethane-based formulations, deliver exceptional thermal conductivity, electrical insulation, and environmental protection. Ideal for applications in the aerospace, automotive, and telecommunications industries, Matrix potting materials ensure reliable, long-lasting protection against environmental factors and thermal management challenges, enhancing the performance and durability of critical electronic assemblies.
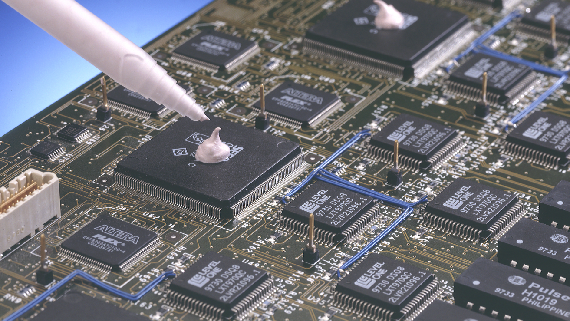
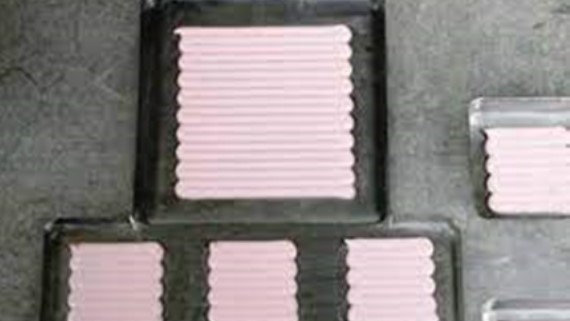
Value Added
Matrix enhances the value of cure-in-place potting materials in-house by tailoring solutions to precise customer needs. This includes customizing material properties, optimizing cure processes, and providing technical expertise. We offer rapid prototyping, supply chain management, and just-in-time delivery, ensuring you receive tailored potting solutions that meet your exact specifications.
Frequently asked questions
If you have a question that is not addressed in our FAQ please click 'Contact Matrix' at the top of the page and submit. We will answer directly and add it to our FAQ to benefit the entire engineering community.
Your vision! Our expertise! Collaborating with engineering teams is what we do best! We listens to your priorities, and create a customized solution tailored to your specific requirements.
1. Epoxy-Based Potting Materials:
- Description: Matrix epoxy-based materials offer exceptional adhesion and high mechanical strength.
- Benefits: Superior protection for electronic components, excellent thermal conductivity, and resistance to environmental factors make them ideal for rugged applications.
2. Silicone-Based Potting Materials:
- Description: Silicone-based materials provide flexibility and resistance to moisture and temperature extremes.
- Benefits: Excellent electrical insulation, thermal stability, and vibration dampening, making them suitable for demanding environments and delicate components.
3. Urethane-Based Potting Materials:
- Description: Matrix urethane-based materials offer good adhesion and flexibility.
- Benefits: They combine mechanical robustness with moisture resistance, making them suitable for a wide range of electronic applications, including sealing and encapsulation.
Each of these cure-in-place potting materials from Matrix serves specific engineering needs, providing tailored solutions for diverse electronic application.
1. Chemical Compatibility:
- Verify compatibility with the materials being potted to prevent chemical reactions or degradation.
2. Curing Process:
- Evaluate curing mechanisms (e.g., heat, UV, moisture) and ensure compatibility with the assembly process.
3. Thermal Conductivity (k):
- Assess the material’s ability to dissipate heat to prevent component overheating.
4. Thermal Expansion Coefficient (CTE):
- Match the CTE of the potting compound with that of the components to minimize stress during thermal cycling.
5. Electrical Insulation Properties:
- Ensure the compound provides electrical insulation to protect sensitive components.
6. Mechanical Strength:
- Consider mechanical properties (e.g., tensile strength, hardness) for component support and protection.
7. Environmental Resistance:
- Assess resistance to environmental factors like moisture, chemicals, and UV radiation.
8. Shrinkage and Expansion:
- Account for any volume changes during curing, which can affect component stability.
9. Adhesion:
- Verify strong adhesion to components and substrates to prevent delamination.
10. Potting Process:
- Evaluate ease of application, potting depth, and potting equipment compatibility.
11. Regulatory Compliance:
- Ensure the compound meets industry-specific standards and regulations, such as RoHS and UL listings.
12. Cost Analysis:
- Consider material and processing costs to align with budget constraints.
13. Service Temperature Range:
- Determine if the compound can withstand the operating temperature range of the application.
14. Pot Life:
- Assess the time available for mixing and potting before the compound cures.
15. Cure Time:
- Evaluate curing time and temperature requirements, as longer cure times can impact production schedules.
16. Reactivity:
- Be aware of any reactivity concerns, especially in applications with sensitive components.
17. Aging and Shelf Life:
- Understand the compound’s shelf life and its performance over time.
By meticulously considering these technical factors, engineers can select the most suitable cure-in-place potting compound to ensure the long-term reliability and performance of electronic assemblies.
Cure-in-place potting compounds are versatile materials used across various industries to address specific technical challenges. Here are some technical examples of industries, problems they solve, and applications:
1. Electronics Encapsulation (e.g., Aerospace):
- Problem: Electronics in aerospace face extreme temperature variations and vibrations.
- Solution: Potting compounds protect components from thermal cycling, vibrations, and moisture ingress.
- Industry: Aerospace, avionics, satellite systems.
2. Automotive Electronics:
- Problem: Automotive electronics require protection against thermal stress and environmental factors.
- Solution: Potting materials shield electronics from temperature extremes, vibrations, and chemicals.
- Industry: Automotive, electric vehicles (EVs).
3. Renewable Energy Systems:
- Problem: Solar inverters and wind turbine controls need protection against harsh outdoor conditions.
- Solution: Potting compounds offer environmental resistance and insulation, ensuring longevity.
- Industry: Renewable energy, solar power, wind energy.
4. Underwater Sensors:
- Problem: Submersible sensors must withstand high pressure and water ingress.
- Solution: Potting materials provide water resistance and protect sensitive electronics.
- Industry: Oceanography, marine exploration.
5. Medical Devices:
- Problem: Medical equipment requires protection from moisture, chemicals, and sterilization processes.
- Solution: Potting compounds safeguard electronics, ensuring reliability and sterility.
- Industry: Healthcare, medical device manufacturing.
6. High-Performance Computing (HPC):
- Problem: HPC systems generate significant heat that can impact component longevity.
- Solution: Potting materials dissipate heat, ensuring stable operation in data centers.
- Industry: Data centers, HPC, telecommunications.
7. Industrial Automation:
- Problem: Industrial control systems need protection against harsh manufacturing environments.
- Solution: Potting compounds shield electronics from dust, chemicals, and vibrations.
- Industry: Manufacturing, industrial automation.
8. LED Lighting:
- Problem: LEDs generate heat that can reduce efficiency and lifespan.
- Solution: Potting materials dissipate heat, prolonging LED life and efficiency.
- Industry: Lighting, architectural lighting.
9. Sensors and Instrumentation:
- Problem: Sensitive sensors require protection against environmental factors.
- Solution: Potting compounds offer insulation and protection for accurate readings.
- Industry: Instrumentation, environmental monitoring.
10. Telecommunications:
- Problem: Telecom equipment faces temperature fluctuations and moisture.
- Solution: Potting materials ensure reliable operation in various weather conditions.
- Industry: Telecommunications, network infrastructure.
Cure-in-place potting compounds play a critical role in protecting electronic components and ensuring their longevity in diverse technical applications across industries.
COMPARE
Compare Options
Click below chart to get a customized chart specific to your application.
1
2
3
1 | 2 | 3 | |
Consideration | Epoxy-Based Compound |
Silicone-Based Compound |
Urethane-Based Compound |
Phase Change Temperature (Tc) | Good | Good | Good |
Latent Heat of Fusion (ΔH) | Good | Moderate | Good |
Thermal Conductivity (k) | Good | Moderate | Good |
Thermal Resistance (R) | Moderate | Good | Moderate |
Cycle Life | Good | Good | Good |
Volume Change | Good | Good | Good |
Chemical Compatibility | Good | Good | Good |
Thermal Stability | Good | Good | Good |
Environmental Impact | Good | Good | Good |
Cost | Good | Good | Good |