Product Description
Matrix UHMW (Ultra-High Molecular Weight Polyethylene) solutions encompass sheets, rods, and tapes, offering engineers exceptional abrasion resistance, low-friction characteristics, and durability. Widely utilized in industries such as conveyor systems, material handling, and food processing, UHMW tapes, in particular, provide efficient wear protection and noise reduction. With outstanding chemical resistance and a low coefficient of friction, these UHMW solutions optimize equipment performance, making them ideal for demanding engineering applications requiring reliable, long-lasting materials.
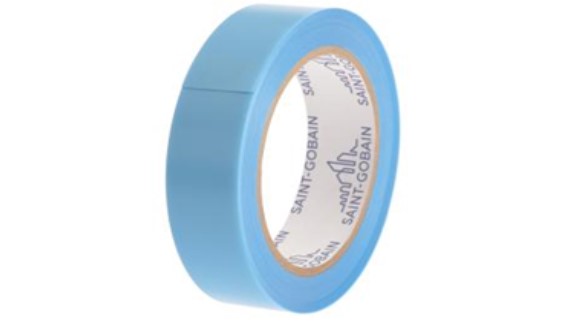
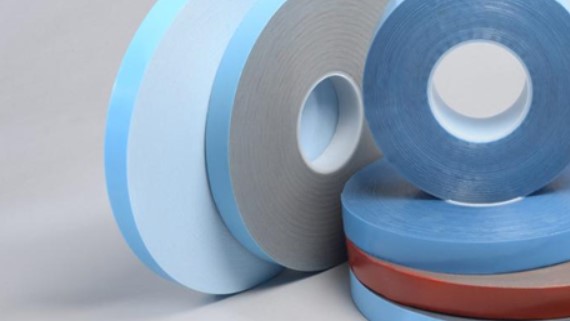
Value Added
Matrix enhances its role as a UHMW (Ultra-High Molecular Weight Polyethylene) partner by leveraging in-house converting expertise like kiss cutting, rotary die cutting, and precision slitting. These advanced techniques enable engineers to access customized UHMW solutions with meticulous precision, ensuring tailored fitment, minimized waste, and maximized performance in demanding technical applications.
Frequently asked questions
If you have a question that is not addressed in our FAQ please click 'Contact Matrix' at the top of the page and submit. We will answer directly and add it to our FAQ to benefit the entire engineering community.
Your vision! Our expertise! Collaborating with engineering teams is what we do best! We listens to your priorities, and create a customized solution tailored to your specific requirements.
1. UHMW Sheets
- Description: Solid UHMW (Ultra-High Molecular Weight Polyethylene) sheets with excellent wear resistance.
- Benefit for Engineers: Exceptional durability and low friction, ideal for lining chutes and hoppers in abrasive environments.
2. UHMW Tapes
- Description: UHMW adhesive tapes with a low coefficient of friction.
- Benefit for Engineers: Effortless application, reducing friction and noise in moving parts like conveyors and chutes.
3. UHMW Custom Fabrications
- Description: Precision-engineered UHMW components tailored to exact specifications.
- Benefit for Engineers: Customization for specialized applications, ensuring precise fit and performance optimization.
4. UHMW Wear Strips
- Description: UHMW wear strips for conveyor and guide rail applications.
- Benefit for Engineers: Enhanced equipment lifespan by reducing wear and maintenance requirements in material handling systems.
5. UHMW Profiles
- Description: UHMW profiles for use as guides and runners.
- Benefit for Engineers: Low-friction, smooth operation, and extended service life in sliding applications.
6. UHMW Liners
- Description: UHMW liners for hoppers, chutes, and bins.
- Benefit for Engineers: Abrasion resistance, reduced material buildup, and increased flow efficiency in bulk material handling.
7. UHMW Bearings
- Description: UHMW bearings for friction-reducing applications.
- Benefit for Engineers: Low friction, self-lubricating properties for extended component life in rotating and sliding mechanisms.
8. UHMW Seals and Gaskets
- Description: UHMW seals and gaskets for sealing applications.
- Benefit for Engineers: Chemical resistance, long-lasting sealing solutions, and reduced maintenance in critical environments.
1. Wear Resistance: Evaluate the UHMW material’s ability to withstand abrasion and wear over time, especially in applications with frequent movement or friction.
2. Coefficient of Friction: Determine the material’s friction characteristics to ensure it aligns with the intended use, whether low friction is needed for ease of movement or high friction for gripping.
3. Chemical Compatibility: Confirm that the UHMW material is resistant to the chemicals, solvents, or fluids it will encounter in the operating environment.
4. Temperature Range: Ensure the chosen UHMW solution can withstand the temperatures within the intended application, from extreme cold to high heat.
5. Load-Bearing Capacity: Consider the application’s weight-bearing requirements and select UHMW with the necessary mechanical strength to support the load.
6. Impact Resistance: Assess the material’s ability to withstand impacts and shocks without deformation or damage, especially in high-impact applications.
7. FDA Compliance: For applications in food processing or pharmaceutical industries, verify that the UHMW material meets regulatory standards, such as FDA approval.
8. Dimensional Stability: Choose UHMW materials that maintain their shape and size under varying conditions to prevent warping or distortion.
9. Customization Options: Determine whether the UHMW solution can be tailored or fabricated to meet specific design requirements for complex or unique applications.
10. Environmental Conditions: Consider any environmental factors, such as exposure to UV radiation, moisture, or outdoor elements, that might affect the UHMW material’s performance over time.
11. Cost and Availability: Assess the cost-effectiveness of the selected UHMW solution in relation to the project budget, as well as its availability from suppliers.
12. Longevity and Maintenance: Evaluate the expected service life of the UHMW material and consider the ease of maintenance and replacement when necessary.
13. Testing and Prototyping: Conduct thorough testing and prototyping to validate the performance of the selected UHMW solution under real-world conditions before full-scale implementation.
1. Conveyor Systems:
- Problem: High friction causing wear and noise in conveyor systems.
- Solution: UHMW tapes with a low coefficient of friction for smoother material transport.
- Industry and Application: Material handling and logistics, reducing wear on conveyor belts and guides.
2. Chute Linings:
- Problem: Abrasive materials causing wear and material buildup in chutes.
- Solution: UHMW tapes as chute liners to reduce friction, minimize material buildup, and enhance flow.
- Industry and Application: Mining, agricultural, and bulk material handling, improving material flow and reducing maintenance.
3. Guide Rails and Rails:
- Problem: High wear and friction in guiding and sliding applications.
- Solution: UHMW tapes as rail covers, minimizing wear and ensuring smooth motion.
- Industry and Application: Manufacturing, packaging, and automation, reducing wear on guide rails and extending equipment life.
4. Packaging Machinery:
- Problem: Packaging equipment parts experiencing excessive friction.
- Solution: UHMW tapes as liners and wear strips to reduce friction, prevent jams, and enhance packaging efficiency.
- Industry and Application: Food, pharmaceutical, and packaging industries, improving productivity and reducing downtime.
5. Automotive Manufacturing:
- Problem: High wear in automotive assembly line components.
- Solution: UHMW tapes as abrasion-resistant wear pads, extending the life of tooling and fixtures.
- Industry and Application: Automotive manufacturing, improving the longevity of assembly line equipment.
6. Print and Paper Industry:
- Problem: Paper sticking to rollers and guides.
- Solution: UHMW tapes on rollers and guides to reduce adhesion and friction, ensuring smooth paper processing.
- Industry and Application: Printing and paper processing, enhancing production quality.
7. Textile Manufacturing:
- Problem: Material sticking and friction in textile machinery.
- Solution: UHMW tapes as anti-friction guides, preventing material snags and improving textile production efficiency.
- Industry and Application: Textile manufacturing, reducing production interruptions.
8. Material Testing Machines:
- Problem: High friction affecting precision in material testing.
- Solution: UHMW tapes on test fixtures to reduce friction and ensure accurate material testing.
- Industry and Application: Material testing laboratories, improving test accuracy.
COMPARE
Compare Options
Click below to get a customized comparison chart tailored to your application.
1
2
3
1 | 2 | 3 | |
Consideration | UHMW Tapes | PTFE Tapes | Nylon Tapes |
Wear Resistance | Very Good | Good | Moderate |
Coefficient of Friction | Very Low | Very Low | Moderate |
Chemical Compatibility | Good | Very Good | Moderate |
Temperature Range | Good | Very Good | Moderate |
Electrical Insulation | Good | Very Good | Moderate |
Adhesion to Substrates | Good | Moderate | Very Good |
Thickness and Durability | Good | Good | Good |
Cost-Effectiveness | Good | Moderate | Good |
Ease of Machining | Good | Moderate | Good |
Customization Options | Good | Good | Good |