Product Description
Matrix conductive plastics feature electrically conductive elastomers and thermoplastic compounds, delivering exceptional EMI shielding and environmental sealing. Engineers benefit from their high conductivity, shielding effectiveness exceeding 100 dB, and resilience against harsh conditions. These materials find widespread use in aerospace, automotive, and electronics industries, where they ensure reliable performance of sensitive electronics, such as connectors, enclosures, and gaskets, while complying with stringent EMI regulations and mitigating electromagnetic interference (EMI) challenges.
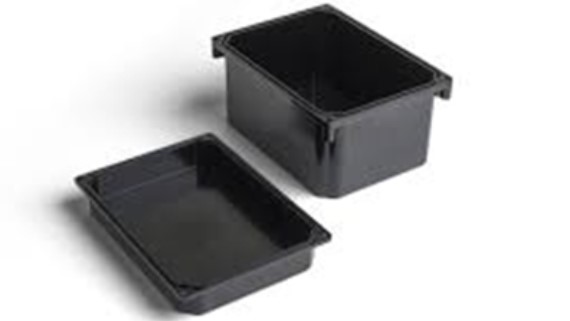
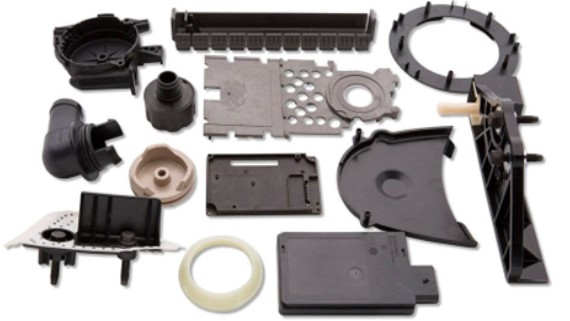
Value Added
Matrix enhances engineering processes by customizing conductive plastics for exact applications. Employing advanced Injection Molding techniques, we optimize material formulations and geometries. This precision ensures that our conductive plastics meet demanding specifications, delivering superior EMI shielding, environmental sealing, and thermal management tailored to your project's specific needs.
Frequently asked questions
If you have a question that is not addressed in our FAQ please click 'Contact Matrix' at the top of the page and submit. We will answer directly and add it to our FAQ to benefit the entire engineering community.
Your vision! Our expertise! Collaborating with engineering teams is what we do best! We listens to your priorities, and create a customized solution tailored to your specific requirements.
1. Electrically Conductive Elastomers
- Description: Elastic compounds filled with conductive particles.
- Benefit: High elasticity and compression set resistance, ideal for sealing and EMI gasket applications, ensuring reliable EMI shielding and environmental sealing.
2. Thermoplastic Conductive Polymers
- Description: Thermoplastic compounds with conductive additives.
- Benefit: Lightweight, easily molded, and cost-effective, suitable for injection molding EMI shielding and static dissipation components.
3. Conductive Silicone Rubbers
- Description: Silicone-based elastomers infused with conductive fillers.
- Benefit: Excellent flexibility and temperature resistance, making them ideal for EMI gaskets, connectors, and seals in extreme environments.
4. Conductive Plastics with Flame Retardancy
- Description: Conductive plastics designed to meet stringent flame retardancy standards.
- Benefit: Ensures compliance with safety regulations while providing EMI shielding and static dissipation in electronics and aerospace applications.
5. Conductive Plastics for Electrostatic Discharge (ESD) Control
- Description: ESD-safe conductive plastics.
- Benefit: Protects sensitive electronic components from electrostatic discharge, preventing damage in manufacturing and electronics assembly.
6. Electrically Conductive Thermosetting Resins
- Description: Thermoset resins with conductive additives.
- Benefit: High heat resistance and dimensional stability, suitable for applications requiring reliable EMI shielding in elevated-temperature environments.
7. Specialty Magnetic Shielding Materials
- Description: Magnetic shielding plastics like Mu-metal composites.
- Benefit: Exceptional magnetic field attenuation, ideal for MRI and sensitive scientific equipment where precision shielding is critical.
8. Flexible Transparent Conductive Films
- Description: Thin, transparent conductive films.
- Benefit: Combine transparency with electrical conductivity, used in touchscreens, displays, and transparent EMI shielding applications.
9. Hybrid Conductive Materials
- Description: Combinations of conductive fillers in various polymer matrices.
- Benefit: Tailored solutions for specific EMI shielding, thermal management, and mechanical requirements in complex applications.
10. Bio-Compatible Conductive Plastics
- Description: Conductive plastics compatible with medical and biotech environments.
- Benefit: Ensures EMI shielding and ESD protection in medical devices and equipment while maintaining biocompatibility for patient safety.
These conductive plastic materials offer engineers a diverse range of options to meet specific technical requirements, whether it’s EMI shielding, environmental sealing, static control, or specialized needs in various industries, including electronics, aerospace, automotive, and healthcare.
When selecting a conductive plastic for an engineering application, the engineering team should consider several important factors to ensure the material meets the project’s requirements:
Electrical Conductivity: Evaluate the material’s electrical conductivity to ensure it meets the required level for EMI shielding or static dissipation.
Shielding Effectiveness: Determine the shielding effectiveness of the conductive plastic at the specific frequencies relevant to the application.
Material Compatibility: Assess the compatibility of the conductive plastic with other materials used in the assembly, such as adhesives, substrates, and enclosures.
Mechanical Properties: Consider the mechanical characteristics, including tensile strength, flexibility, and impact resistance, to ensure the material can withstand environmental and mechanical stresses.
Temperature Range: Determine the operating temperature range of the conductive plastic and verify it matches the application’s thermal requirements.
Chemical Resistance: Evaluate the material’s resistance to chemicals, solvents, and environmental factors to ensure long-term durability.
Environmental Sealing: If needed, assess the material’s capability to provide environmental sealing to protect against dust, moisture, and contaminants.
Dimensional Stability: Ensure the conductive plastic maintains its shape and dimensions under varying conditions, particularly in applications with tight tolerances.
Regulatory Compliance: Verify that the material complies with industry standards and regulations, especially in safety-critical applications like aerospace or medical devices.
Cost and Availability: Consider the material’s cost and availability in the required quantities to align with project budgets and production schedules.
Ease of Processing: Evaluate how easily the conductive plastic can be processed and integrated into the manufacturing process, including factors like molding, bonding, and assembly.
Surface Finish: Assess the surface finish of the material to ensure it meets cosmetic and tactile requirements, especially in consumer electronics or medical devices.
Static Control: If relevant, confirm that the material provides effective static charge dissipation or ESD protection.
Biocompatibility: In medical or biotech applications, ensure the conductive plastic is biocompatible and safe for use in contact with the human body.
Lifecycle Considerations: Consider the expected service life of the material and whether it will meet long-term performance requirements.
Recyclability: Evaluate the material’s recyclability and sustainability in line with environmental goals.
Supplier and Technical Support: Consider the reputation of the material supplier and their ability to provide technical support and customization if necessary.
By carefully assessing these factors, engineering teams can make informed decisions when selecting a conductive plastic material that aligns with the specific needs and performance requirements of their project.
Conductive plastics find common use in various technical applications across industries to address specific problems. Here are some examples:
1. Electromagnetic Interference (EMI) Shielding in Electronics
- Problem: Sensitive electronic components are susceptible to EMI, leading to performance degradation.
- Solution: Conductive plastics, in the form of enclosures, gaskets, and connectors, provide EMI shielding for consumer electronics, aerospace, and automotive applications. For instance, smartphone cases made from conductive plastics shield against unwanted electromagnetic interference (EMI) (Industry: Electronics).
2. Static Dissipation in Cleanroom Environments
- Problem: Static charge accumulation can damage sensitive semiconductor devices and contaminate cleanroom environments.
- Solution: Conductive plastics are used in flooring, workstations, and equipment to dissipate static charges safely, maintaining the integrity of semiconductor manufacturing processes (Industry: Semiconductor Manufacturing).
3. Aircraft Fuel Systems
- Problem: Fuel systems in aircraft require protection against electrostatic discharge (ESD) to prevent potential explosions.
- Solution: Conductive plastics are employed in fuel system components to safely dissipate static charges and mitigate ESD risks (Industry: Aerospace).
4. Medical Device Enclosures
- Problem: Medical devices require both EMI shielding and biocompatibility.
- Solution: Conductive plastics with specialized formulations cater to medical device enclosures, ensuring EMI protection and compliance with biocompatibility standards (Industry: Healthcare and Medical Devices).
5. Automotive Fuel Tanks
- Problem: Electrostatic buildup in fuel tanks poses a fire hazard.
- Solution: Conductive plastics are used in fuel tank components to prevent electrostatic discharge, enhancing automotive safety (Industry: Automotive).
6. Electrostatic Spray Painting Equipment
- Problem: Accumulated static charges can cause defects in painted surfaces.
- Solution: Conductive plastics in the form of nozzles, hoses, and components prevent static buildup, ensuring uniform coating in painting equipment (Industry: Manufacturing and Automotive).
7. Biotech and Laboratory Equipment
- Problem: Sensitive biotech equipment requires EMI shielding and static control.
- Solution: Conductive plastics are used in enclosures and components to provide both EMI shielding and static dissipation, preserving the integrity of research and testing (Industry: Biotechnology and Research Laboratories).
8. Solar Panel Manufacturing
- Problem: Electrostatic charges can attract dust and particles on solar panels, reducing efficiency.
- Solution: Conductive plastics in panel frames and coatings prevent static buildup, maintaining solar panel performance (Industry: Renewable Energy).
9. Explosive Atmospheres
- Problem: Electrostatic discharge can ignite flammable materials in explosive environments.
- Solution: Conductive plastics in equipment and machinery components help prevent ESD incidents in hazardous industries such as petrochemicals and mining (Industry: Hazardous Materials Handling).
10. Electrostatic Sensitive Devices (ESD) Packaging
- Problem: ESD can damage sensitive electronic components during handling and transportation.
- Solution: Conductive plastic packaging materials, such as trays and bags, provide protection against ESD, preserving the integrity of electronic components (Industry: Electronics and Semiconductor Manufacturing).
In each of these applications and industries, conductive plastics are chosen for their ability to solve specific technical challenges related to EMI shielding, static dissipation, and safety, contributing to the overall performance, reliability, and safety of critical systems and equipment.
COMPARE
Compare Options
Click below to get a customized comparison chart tailored to your application.
1
2
3
1 | 2 | 3 | |
Consideration | Electrically Conductive Elastomers |
Thermoplastic Conductive Polymers |
Conductive Silicone Rubbers |
Electrical Conductivity (S/m) | Very Good | Good | Good |
EMI Shielding Effectiveness | Very Good | Good | Good |
Flexibility | Very Good | Good | Very Good |
Temperature Range | Good | Very Good | Very Good |
Chemical Resistance | Good | Good | Very Good |
Environmental Sealing | Very Good | Moderate | Good |
Mechanical Properties | Very Good | Good | Good |
Biocompatibility | Moderate | Moderate | Good |
Ease of Processing | Good | Very Good | Good |
Regulatory Compliance | Very Good | Good | Good |