Product Description
Matrix sub miniature connectors series, provide engineers with high-density, reliable connectivity solutions for demanding applications. These connectors boast rugged designs, IP68 sealing, and customizable configurations, making them ideal for industries like medical devices, aerospace, and robotics. With options for power, signal, and data transmission, Matrix subminiature connectors offer exceptional performance, EMI/RFI protection, and compact form factors, enabling engineers to optimize space and performance in critical systems.
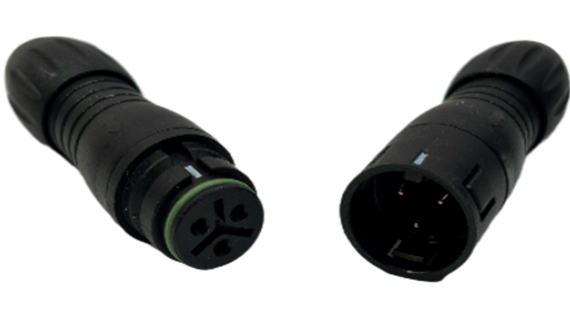
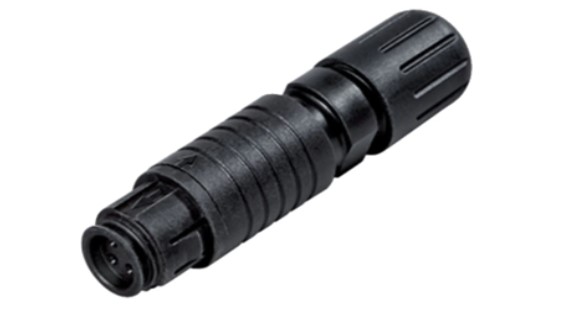
Value Added
Matrix adds significant value to engineering teams by offering not only high-quality connectors but also fully customized harnesses and assemblies. This comprehensive approach streamlines integration, ensures compatibility, and minimizes potential points of failure. Matrix specializes in ruggedizing these solutions, employing advanced materials and techniques to enhance durability, shielding, and environmental resilience, ultimately optimizing performance in demanding industrial and military applications.
Frequently asked questions
If you have a question that is not addressed in our FAQ please click 'Contact Matrix' at the top of the page and submit. We will answer directly and add it to our FAQ to benefit the entire engineering community.
Your vision! Our expertise! Collaborating with engineering teams is what we do best! We listens to your priorities, and create a customized solution tailored to your specific requirements.
1. Push-Pull Subminiature Connectors
- Description: Push-pull subminiature connectors, like LEMO connectors, feature a self-latching mechanism for secure mating and demating.
- Primary Benefit for Engineers: Engineers appreciate their robust and quick-connect design, which ensures dependable connections in critical applications, saving time and improving reliability.
2. Snap-In Subminiature Connectors
- Description: Snap-in subminiature connectors, such as SMB connectors, utilize a snap-on coupling mechanism for efficient assembly.
- Primary Benefit for Engineers: These connectors simplify installation, reducing labor costs, and offer excellent RF performance for high-frequency applications.
3. Screw-Lock Subminiature Connectors
- Description: Screw-lock subminiature connectors, like TNC connectors, employ threaded coupling to ensure secure connections.
- Primary Benefit for Engineers: Engineers value their high mechanical stability, which prevents accidental disconnection and maintains signal integrity.
4. Miniature Circular Connectors
- Description: Miniature circular connectors, e.g., MIL-DTL-38999, provide compact, circular-shaped designs suitable for aerospace and military applications.
- Primary Benefit for Engineers: They offer ruggedness and versatility, enabling engineers to accommodate a wide range of signals, power, and data connections in harsh environments.
5. Fiber Optic Subminiature Connectors
- Description: Fiber optic subminiature connectors, like LC connectors, enable high-speed data transmission via optical fibers.
- Primary Benefit for Engineers: Engineers benefit from their bandwidth and immunity to electromagnetic interference, making them ideal for data-intensive applications in telecommunications and data centers.
6. Micro-D Connectors
- Description: Micro-D connectors feature compact rectangular shapes, often used in aerospace and military electronics.
- Primary Benefit for Engineers: Their miniaturized form factor allows engineers to save space while accommodating a wide range of signal and power connections in constrained environments.
7. High-Temperature Subminiature Connectors
- Description: High-temperature subminiature connectors, such as ceramic connectors, withstand extreme heat conditions.
- Primary Benefit for Engineers: These connectors ensure reliability in high-temperature environments, crucial for aerospace, automotive, and industrial applications.
8. Harsh Environment Specialty Connectors
- Description: Specialty connectors, like Amphenol’s MIL-DTL-38999 Series III, are designed for rugged and demanding environments.
- Primary Benefit for Engineers: Engineers appreciate their resistance to moisture, chemicals, and physical damage, ensuring consistent performance in challenging applications, such as military and industrial settings.
1. Electrical Properties:
- Impedance Matching: Ensure the connector’s characteristic impedance matches the transmission line to minimize signal reflection and loss.
- Voltage and Current Ratings: Select connectors capable of handling the required voltage and current levels without voltage drop or overheating.
2. Signal Integrity:
- Signal Frequency: Choose connectors designed for the frequency range of the signals being transmitted to maintain signal integrity.
- Insertion Loss and Return Loss: Evaluate connectors for low insertion loss and high return loss to minimize signal degradation.
3. Environmental Conditions:
- Operating Temperature: Consider the temperature range in which the connectors will operate and select those rated to withstand extreme temperatures.
- Moisture and Contaminant Resistance: For harsh environments, opt for connectors with adequate sealing to prevent moisture and contaminants from compromising performance.
4. Mechanical Durability:
- Mating Cycles: Assess the connector’s durability in terms of mating and unmating cycles, especially in applications where frequent connections are required.
- Vibration and Shock Resistance: Ensure connectors can withstand mechanical stresses, such as vibrations and shocks, common in aerospace and automotive applications.
5. Size and Form Factor:
- Space Constraints: Consider the available space for connector installation and select compact sub-miniature connectors that fit within the designated area.
- Connector Type: Choose connectors that match the form factor and interface requirements of the equipment and system.
6. EMI/RFI Shielding:
- Electromagnetic Compatibility (EMC): Assess the connector’s effectiveness in providing electromagnetic interference (EMI) and radiofrequency interference (RFI) shielding to prevent signal interference.
7. Material Compatibility:
- Chemical Resistance: Ensure connectors are resistant to chemicals or substances present in the environment or during cleaning procedures.
- Corrosion Resistance: Evaluate connectors for resistance to corrosion in corrosive environments.
8. Customization and Special Features:
- Contact Arrangement: Depending on the application, consider the number and arrangement of contacts, including coaxial, signal, power, and data contacts.
- Keying and Polarization: Use connectors with keying or polarization features to prevent incorrect mating.
- Locking Mechanism: Assess the need for locking mechanisms (e.g., push-pull, screw lock) to secure connections in high-vibration scenarios.
9. Compliance and Standards:
- Industry Standards: Ensure connectors meet relevant industry and military standards, such as MIL-DTL-38999, to guarantee interoperability and performance.
- Safety Certifications: Verify compliance with safety certifications and regulations, particularly in industries like healthcare and aerospace.
10. Cost and Availability:
- Cost-Effectiveness: Consider the overall cost of connectors, including procurement, installation, and maintenance.
- Availability: Ensure a stable supply chain to prevent production disruptions due to component shortages.
1. Medical Devices
- Problem: Miniaturization is crucial for wearable medical devices and minimally invasive surgical tools, but they require reliable and compact connectors.
- Solution: Sub-miniature connectors like Fischer MiniMaxâ„¢ are used in medical applications such as endoscopes and patient monitoring equipment, providing small form factors and secure connections. [Reference: Medical Electronics]
2. Aerospace and Aviation
- Problem: Space constraints and weight limitations demand lightweight connectors that can withstand harsh environmental conditions.
- Solution: Micro-D connectors are employed in avionics systems and satellites due to their small size, lightweight design, and robust construction, ensuring reliability in aerospace applications. [Reference: Aerospace Engineering]
3. Automotive Electronics
- Problem: Automotive electronics require connectors that can handle vibration, shock, and temperature variations.
- Solution: Sub-miniature connectors like Molex’s MX150â„¢ are used in automotive control units and sensors, offering durability and resistance to harsh automotive environments. [Reference: Automotive Engineering]
4. Telecommunications
- Problem: High-speed data transmission demands connectors that maintain signal integrity and minimize electromagnetic interference.
- Solution: Fiber optic sub-miniature connectors, such as LC connectors, provide low-loss, high-bandwidth connections for data centers, telecommunications equipment, and networking applications. [Reference: Telecommunications]
5. Industrial Automation
- Problem: Industrial automation systems require connectors that can handle high-speed data, power, and signal connections in demanding industrial environments.
- Solution: Miniature circular connectors are commonly used in industrial automation machinery and robotics, offering ruggedness and versatility for reliable data and power transmission. [Reference: Industrial Automation]
6. Defense and Military Electronics
- Problem: Military applications demand connectors that can withstand extreme environmental conditions, including temperature variations, shock, and moisture.
- Solution: Specialty connectors like MIL-DTL-38999 Series III connectors are utilized in military equipment, providing robustness and compliance with military standards for harsh field deployments. [Reference: Defense Industry]
7. Oil and Gas Exploration
- Problem: Oil and gas exploration requires connectors that can resist corrosion, high temperatures, and pressure differentials.
- Solution: High-temperature and corrosion-resistant sub-miniature connectors are used in downhole tools and drilling equipment, ensuring reliability in extreme oil and gas environments. [Reference: Oil and Gas Industry]
8. Consumer Electronics
- Problem: Miniaturization is essential in consumer electronics, such as smartphones and wearables, to create compact and portable devices.
- Solution: Push-pull sub-miniature connectors are used in consumer electronics, offering space-saving and reliable interconnect solutions for various portable devices. [Reference: Consumer Electronics]
COMPARE
Compare Options
Click below to get a customized comparison chart tailored to your application.
1
2
3
1 | 2 | 3 | |
Consideration | Brand A | Brand B | Brand C |
Electrical Properties | Very Good | Good | Moderate |
Signal Integrity | Very Good | Good | Moderate |
Environmental Conditions | Good | Moderate | Very Good |
Mechanical Durability | Very Good | Good | Moderate |
Size and Form Factor | Good | Very Good | Moderate |
EMI/RFI Shielding | Good | Very Good | Moderate |
Material Compatibility | Good | Very Good | Moderate |
Customization and Special Features | Moderate | Good | Very Good |
Compliance and Standards | Very Good | Good | Moderate |
Cost and Availability | Moderate | Good | Very Good |