Product Description
Matrix’s glass foil tapes encompass a range, including aluminum foil-coated, copper foil-coated, and vermiculite-coated options, prized for their exceptional thermal conductivity, electrical shielding, and fire-resistant properties. Engineers benefit from these tapes' ability to efficiently dissipate heat, provide EMI/RFI shielding, and enhance fire safety. These solutions find application in aerospace, electronics, and construction, ensuring optimal performance in demanding engineering environments. Matrix also offers additional glass foil solutions to cater to various specialized industrial needs.
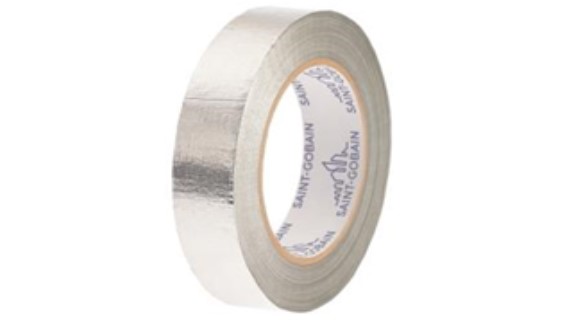
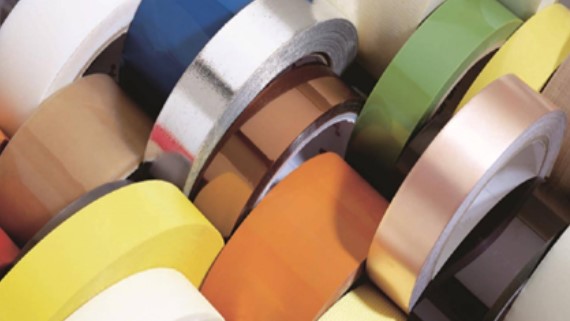
Value Added
Enhances its role as a glass-foil tape partner through in-house converting expertise, including kiss cutting, rotary die cutting, and precision slitting. These advanced techniques allow engineers to access customized glass-foil tape solutions with exacting precision, ensuring tailored fitment, minimal waste, and optimized performance in demanding technical applications.
Frequently asked questions
If you have a question that is not addressed in our FAQ please click 'Contact Matrix' at the top of the page and submit. We will answer directly and add it to our FAQ to benefit the entire engineering community.
Your vision! Our expertise! Collaborating with engineering teams is what we do best! We listens to your priorities, and create a customized solution tailored to your specific requirements.
1. Aluminum Foil-Coated Glass Foil Tape:
- Description: Glass foil tape with an aluminum foil backing.
- Benefit for Engineers:Exceptional thermal conductivity, effective heat dissipation, and resistance to high temperatures, making it ideal for thermal management and insulation in electronic components.
2. Copper Foil-Coated Glass Foil Tape:
- Description: Glass foil tape with a copper foil backing.
- Benefit for Engineers: Excellent electrical conductivity, EMI/RFI shielding, and grounding capabilities, essential for electronics and electrical applications.
3. Vermiculite-Coated Glass Foil Tape:
- Description: Glass foil tape with a vermiculite coating.
- Benefit for Engineers: Enhanced fire resistance, insulation, and protection against heat and flames, suitable for fireproofing and high-temperature applications.
4. Silver Foil-Coated Glass Foil Tape:
- Description: Glass foil tape with a silver foil backing.
- Benefit for Engineers: Superior electrical conductivity, EMI/RFI shielding, and high thermal conductivity, ideal for advanced electronics and telecommunications.
5. Heat-Treated Glass Foil Tape:
- Description: Glass foil tape subjected to heat treatment for improved mechanical properties.
- Benefit for Engineers:Enhanced tensile strength, reduced fraying, and increased durability, making it excellent for reinforcing and insulating applications.
1. Tempreature Resistance: Verify that the tape can withstand the operating temperatures within the intended environment, including extreme heat or cold.
2. Electrical Properties: Evaluate the tape’s electrical insulation or conductivity properties based on the application’s electrical requirements.
3. Flame Resistance: Assess the tape’s flame-retardant capabilities, especially if fireproofing or heat resistance is essential.
4. Chemical Compatibility: Confirm that the tape is resistant to chemicals, solvents, or substances it may come into contact with during operation.
5. Adhesive Type: Consider the type of adhesive used and its compatibility with the substrate, as well as its adhesion strength and longevity.
6. Conformability: Evaluate the tape’s ability to conform to irregular shapes or surfaces, as it may impact its suitability for specific applications.
7. Thickness and Durability: Examine the tape’s thickness and overall durability, ensuring it meets the mechanical requirements of the application.
8. Cost-Effectiveness: Assess the cost of the tape in relation to the project budget, taking into account long-term performance and value.
9. Customization Options: Determine whether the tape can be customized or fabricated to fit specific dimensions or requirements.
10. EMI/RFI Shielding: If required, verify that the tape offers effective EMI/RFI shielding for sensitive electronic components.
11. Surface Preparation: Consider any necessary surface preparation for optimal adhesion, such as substrate cleanliness and roughness.
12. Regulatory Compliance: Ensure that the selected tape complies with industry-specific regulations, standards, or certifications.
13. Environmental Conditions: Account for environmental factors, such as exposure to UV radiation, moisture, or outdoor elements, that may impact tape performance.
14. Longevity and Maintenance: Evaluate the expected service life of the tape and ease of maintenance or replacement when necessary.
15. Testing and Prototyping: Conduct thorough testing and prototyping to validate the tape’s performance under real-world conditions before full-scale implementation.
1. EMI/RFI Shielding in Electronics:
- Problem: Prevent electromagnetic interference and radiofrequency interference.
- Solution: Copper or silver foil-coated glass foil tapes provide effective shielding.
- Industry and Application: Electronics, telecommunications, aerospace.
2. Thermal Management in Electronics:
- Problem: Efficient heat dissipation in electronic devices.
- Solution: Aluminum foil-coated glass foil tapes with high thermal conductivity.
- Industry and Application: Electronics manufacturing, circuit boards.
3. Fireproofing and Heat Insulation:
- Problem: Protection against high temperatures and fire hazards.
- Solution: Vermiculite-coated glass foil tapes offer enhanced fire resistance.
- Industry and Application: Construction, industrial furnaces, automotive fire barriers.
4. High-Temperature Gasketing:
- Problem: Create heat-resistant seals.
- Solution: Aluminum or copper foil-coated tapes provide reliable gasketing.
- Industry and Application: Petrochemical, manufacturing, high-temperature sealing.
5. Advanced Electronics and Aerospace:
- Problem: Demand for superior electrical conductivity and EMI shielding.
- Solution: Silver foil-coated glass foil tapes excel in high-performance circuitry.
- Industry and Application: Aerospace, advanced electronics, telecommunications.
6. Reinforcement and Structural Bonding:
- Problem: Need for mechanical strength and reinforcement.
- Solution: Heat-treated glass foil tapes offer enhanced tensile strength.
- Industry and Application: Aerospace, composites manufacturing, structural reinforcement.
7. Cryogenic Insulation:
- Problem: Insulation at extremely low temperatures.
- Solution: Aluminum or copper foil-coated tapes provide thermal stability.
- Industry and Application: Cryogenics, space exploration.
8. HVAC Duct Sealing:
- Problem: Air leakage and insulation in heating, ventilation, and air conditioning systems.
- Solution: Aluminum foil-coated tapes for sealing and insulation.
- Industry and Application: HVAC systems, construction.
9. Oil and Gas Pipeline Insulation:
- Problem: Protecting pipelines from corrosion and maintaining insulation.
- Solution: Copper or aluminum foil-coated tapes for insulation and corrosion resistance.
- Industry and Application: Oil and gas pipelines, petrochemical.
10. Aircraft Interior Fireproofing:
- Problem: Fire safety and interior protection in aircraft.
- Solution: Vermiculite-coated tapes for fireproofing.
- Industry and Application: Aerospace, aviation.
COMPARE
Compare Options
Click below to get a customized comparison chart tailored to your application.
1
2
3
1 | 2 | 3 | |
Consideration | Aluminum Foil-Coated Glass Foil Tape | Copper Foil-Coated Glass Foil Tape | Kapton Tapes |
Temperature Resistance | Very Good | Very Good | Very Good |
Electrical Insulation | Good | Very Good | Very Good |
Flame Resistance | Good | Good | Good |
Chemical Resistance | Good | Very Good | Moderate |
Adhesive Strength | Good | Good | Good |
Conformability | Good | Moderate | Good |
Thickness and Durability | Good | Good | Good |
Cost-Effectiveness | Good | Moderate | Moderate |
Customization Options | Good | Good | Good |
EMI/RFI Shielding | Moderate | Good | Good |