Product Description
Matrix conductive greases come in various types optimized for thermal and electrical conductivity. These greases enhance efficiency and reliability by facilitating superior heat dissipation and electrical connections in electronic devices, thereby extending their operational lifespan. Common applications include power electronics, LED lighting, semiconductor devices, and various electronic assemblies, where Matrix conductive greases help engineers manage heat and maintain optimal performance, especially in challenging environmental conditions.
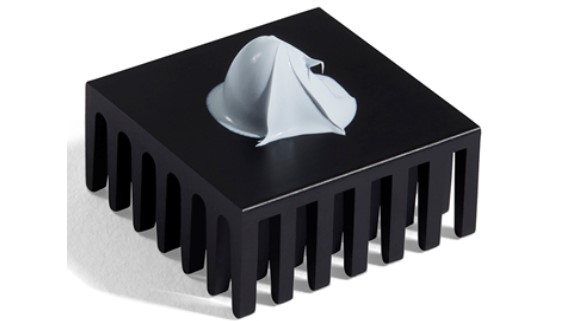
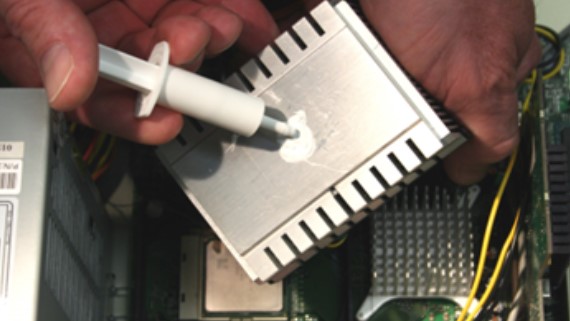
Value Added
Matrix excels in customizing conductive grease solutions to precisely match customers' application needs. By collaborating closely with clients, we tailor the grease formulation to their unique specifications. This includes addressing PCB integration and on-site application, ensuring a seamless fit into their manufacturing supply chain. Our commitment to quality and reliability makes Matrix a trusted partner in enhancing product performance, thermal management, and overall manufacturing efficiency.
Frequently asked questions
If you have a question that is not addressed in our FAQ please click 'Contact Matrix' at the top of the page and submit. We will answer directly and add it to our FAQ to benefit the entire engineering community.
Your vision! Our expertise! Collaborating with engineering teams is what we do best! We listens to your priorities, and create a customized solution tailored to your specific requirements.
Chomerics offers various types of conductive greases, each tailored to specific applications and engineering challenges:
CHO-THERM®: These thermally conductive greases excel in heat management, ensuring efficient transfer of heat from components to heat sinks, addressing the problem of thermal dissipation in electronics.
CHO-BOND®: Electrically conductive greases aid in creating reliable electrical connections, mitigating the challenge of maintaining consistent electrical conductivity in connectors, switches, and contacts.
CHO-LUBE®: Lubricating conductive greases reduce friction and wear in moving parts while maintaining electrical conductivity, solving problems related to mechanical wear and electrical performance in electromechanical devices.
CHO-WAVE®: These microwave absorber greases absorb and dissipate electromagnetic energy, addressing challenges associated with EMI/RFI interference in high-frequency applications.
CHO-SEAL®: EMI shielding conductive greases provide a reliable solution for sealing and shielding electronic enclosures, effectively preventing electromagnetic interference and minimizing radiation issues.
CHOFORM®: Form-in-place conductive greases offer versatility in application, conforming to complex and irregular surfaces, solving challenges in sealing and grounding in various electronic systems.
Application Requirements: Understand the specific needs of the application, including thermal, electrical, mechanical, and environmental requirements.
Material Compatibility: Ensure that the conductive grease is compatible with the materials and components it will come into contact with, such as metals, plastics, or elastomers.
Conductivity Type: Choose the appropriate type of conductive grease (thermal, electrical, or both) based on the intended purpose.
Temperature Range: Consider the operating temperature range and select a grease that can perform within those conditions without losing its properties.
Environmental Conditions: Account for exposure to moisture, chemicals, UV radiation, and other environmental factors, and choose a grease that can withstand these conditions.
Application Method: Determine the most suitable application method, whether it’s manual dispensing, automated equipment, or form-in-place dispensing.
Curing or Drying Time: Understand the grease’s curing or drying time, which may affect production timelines and process efficiency.
Consistency and Viscosity: Choose the appropriate grease consistency and viscosity to ensure proper coverage and ease of application.
Electromagnetic Compatibility (EMC): Consider the grease’s impact on electromagnetic compatibility (EMC) and ensure it complies with relevant EMC standards.
Cleaning and Maintenance: Evaluate ease of cleaning and the long-term maintenance requirements associated with the chosen conductive grease.
Regulatory Compliance: Ensure that the selected grease meets relevant industry and safety regulations, such as RoHS, REACH, and UL.
Quality Control: Establish quality control and testing protocols to verify that the chosen grease consistently meets performance specifications.
Documentation: Maintain detailed records and documentation of the grease’s properties, application procedures, and any special instructions for future reference.
COMPARE
Compare Options
Empower your decision with a tailored comparison chart for the perfect application fit. Compare specifications, brands, and pricing.
1
2
3
1 | 2 | 3 | |
Silver-Based Conductive Grease | Carbon-Based Conductive Grease | Silicone-Based Conductive Grease | |
Electrical Conductivity | High | Medium | Low |
Thermal Conductivity | High | Medium | Low |
Stability | High | Medium | Low |
Operating Temperature | Wide range | Moderate Range | Moderate Range |
Compatibility | Metal Substrates | Wide range of substrates | Plastics and elastomers |
Corrosion Resistance | High | Low | Moderate |
Environmental Impact | Low | Moderate | Low |
Cost | High | Low | Moderate |
Application Method | Dispensing or brushing | Dispensing or brushing | Dispensing or brushing |
Shelf Life | Long | Moderate | Moderate |