Product Description
Matrix thermal gap pads are high-performance, engineering-grade materials designed to efficiently transfer heat in electronic assemblies. These pads come in silicone-based, acrylic-based and phase change material options. With varying durometer levels and impressive w/m-k performance, they provide precise gap filling and conformability, ensuring reliable thermal management in industries like electronics, automotive, and defense. Engineers benefit from improved thermal conductivity, reduced thermal resistance, and simplified assembly processes, ultimately enhancing product reliability and performance.
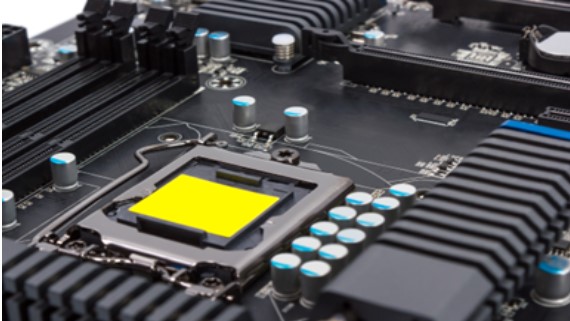
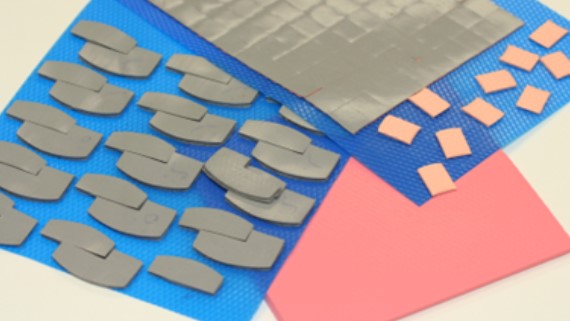
Value Added
Matrix takes pride in fabricating thermal gap pads in-house, ensuring quality control, customization, and efficient production to meet specific customer requirements. Customize your gap pad by adjusting shape, thickness, material composition, adhesive backing, carrier, and compliance. By tailoring a solution to your unique application needs, you can more effectively address thermal challenges, improving overall system reliability and performance.
Frequently asked questions
If you have a question that is not addressed in our FAQ please click 'Contact Matrix' at the top of the page and submit. We will answer directly and add it to our FAQ to benefit the entire engineering community.
Your vision! Our expertise! Collaborating with engineering teams is what we do best! We listens to your priorities, and create a customized solution tailored to your specific requirements.
1. Silicone-Based Gap Pads:
- Description: Silicone-based gap pads are highly conformable thermal interface materials with typical thermal conductivities ranging from 1.0 to 3.0 W/m·K.
- Benefit: These pads offer excellent electrical insulation, low compression force requirements, and good thermal stability, making them suitable for various electronic applications.
2. Acrylic-Based Gap Pads:
- Description: Acrylic-based gap pads exhibit thermal conductivities typically between 1.0 and 2.0 W/m·K.
- Benefit: These pads are known for their low outgassing properties, making them suitable for applications in space or vacuum environments, where outgassing can be critical.
3. Phase Change Gap Pads:
- Description: Phase change gap pads are designed to transition from a solid to a soft, conformable state at a specific temperature (e.g., 50°C to 60°C).
- Benefit: These pads provide precise gap filling and enhanced thermal performance when they change phase, ensuring optimal thermal management in applications where temperature fluctuations are common.
4. High Thermal Conductivity Gap Pads:
- Description: Some specialized gap pads offer extremely high thermal conductivity, exceeding 6.0 W/m·K.
- Benefit: These high-conductivity pads are ideal for applications requiring superior heat dissipation, such as high-power electronics or LED lighting, ensuring efficient thermal transfer and reduced component temperature.
5. Soft Durometer Gap Pads:
- Description: Soft durometer gap pads have a lower hardness, typically below 30 Shore OO, allowing for greater conformability.
- Benefit: These pads offer improved contact in uneven surfaces and delicate components, reducing the risk of damage and enhancing thermal performance in sensitive applications.
6. Graphite-Based Gap Pads:
- Description: Gap pads containing a high percentage of graphite particles, which significantly enhance thermal conductivity.
- Benefit: Ideal for applications where extremely high thermal performance is required, with thermal conductivities often exceeding 10 W/m·K.
7. Ceramic-Filled Gap Pads:
- Description: Gap pads containing ceramic fillers to improve thermal conductivity while maintaining good electrical insulation.
- Benefit: Suited for applications that demand a balance between thermal performance and electrical isolation, such as power electronics.
8. Flame-Retardant Gap Pads:
- Description: Gap pads designed with flame-retardant additives to meet stringent safety requirements.
- Benefit: Suitable for applications where fire resistance and compliance with safety standards are critical, such as in the aerospace and transportation industries.
9. Low-Outgassing Gap Pads:
- Description: Gap pads engineered to emit minimal volatile organic compounds (VOCs) and outgassing.
- Benefit: Vital for space, aerospace, and vacuum applications where outgassing can lead to contamination and equipment malfunction.
10. Customized Gap Pads:
- Description: Tailored thermal gap pad materials designed to meet specific customer requirements, including unique thermal conductivities, durometer levels, and other properties.
- Benefit: Provides engineers with bespoke solutions for challenging or specialized applications.
1. Thermal Conductivity (k): Evaluate the gap pad’s thermal conductivity to ensure it aligns with the heat transfer requirements of the application. A higher thermal conductivity facilitates better heat dissipation.
2. Material Composition: Choose a gap pad material based on its thermal properties, dielectric strength, and chemical resistance. Options include silicone-based, non-silicone-based, or electrically conductive materials.
3. Compliance (Hardness): Consider the compliance or hardness of the gap pad. A compliant pad can conform to surface irregularities and fill gaps effectively, while a harder pad may be necessary for specific applications.
4. Thickness (d): Select the optimal thickness of the gap pad to achieve the desired thermal resistance (Rth) and ensure proper contact between the components.
5. Customization: Assess the manufacturer’s ability to customize the gap pad in terms of size, shape, cutouts, and any additional features to fit the application’s unique geometry.
6. Environmental Factors: Account for the operating temperature range, exposure to chemicals, moisture resistance, and potential degradation over time due to environmental factors.
7. Regulatory Compliance: Verify that the selected gap pad complies with industry standards, safety regulations, and requirements specific to the application, such as UL listings for electrical safety.
8. Cost-Benefit Analysis: Perform a cost-benefit analysis to determine the most cost-effective solution that meets thermal requirements while staying within budget constraints.
9. Ease of Installation: Consider the ease of installation and whether the gap pad requires additional adhesive layers or mechanical fasteners for secure attachment.
10. Compatibility: Ensure compatibility with adjacent components, such as heat sinks, electronic devices, and materials like PCBs, to prevent adverse interactions or thermal mismatch.
11. Performance Under Load: Evaluate how the gap pad performs under varying loads and compression forces, especially in applications with dynamic or changing conditions.
12. Reliability and Longevity: Assess the long-term reliability of the gap pad material, including its thermal stability and resistance to wear, tear, and degradation over time.
Thermal gap pads find widespread use in various industries and applications, primarily to address thermal management challenges. Here are some common applications along with the problems they solve:
1. Electronics and Semiconductor Industry:
- Problem: Electronic components generate heat during operation, leading to thermal issues like overheating and reduced performance.
- Application: Thermal gap pads are used between microprocessors, integrated circuits (ICs), power devices, and heat sinks to improve heat transfer, reduce thermal resistance, and maintain optimal operating temperatures.
2. Automotive Electronics:
- Problem: Increasing electronic content in vehicles generates heat, risking component failure and reduced reliability.
- Application: Gap pads are applied in automotive control units, LED lighting systems, and battery management systems to dissipate heat, ensuring the longevity and reliability of electronic components.
3. Telecommunications:
- Problem: Telecommunications equipment, such as routers and switches, generates significant heat during data processing.
- Application: Gap pads help manage heat in these devices, preventing overheating and ensuring uninterrupted communication.
4. LED Lighting:
- Problem: High-brightness LEDs generate substantial heat, which can lead to premature LED failure and reduced luminosity.
- Application: Gap pads are used in LED assemblies to transfer heat away from the LEDs, maintaining brightness and extending the lifespan of lighting systems.
5. Aerospace and Defense:
- Problem: Aircraft and defense systems operate in extreme conditions, and excess heat can compromise performance.
- Application: Thermal gap pads are employed in avionics, radar systems, and military electronics to mitigate thermal issues and enhance reliability in challenging environments.
6. Medical Devices:
- Problem: Medical equipment, especially those with high-performance computing components, can generate heat that affects patient safety and device operation.
- Application: Gap pads are utilized in medical devices like MRI machines and ultrasound equipment to manage heat and ensure stable and safe operation.
7. Renewable Energy:
- Problem: Solar inverters and wind turbine controllers must handle high-power levels, leading to substantial heat generation.
- Application: Gap pads are used to dissipate heat in renewable energy infrastructure, improving the efficiency and lifespan of power electronics.
8. Consumer Electronics:
- Problem: Laptops, smartphones, and gaming consoles generate heat during intensive use, which can result in discomfort and reduced device lifespan.
- Application: Gap pads are applied in consumer electronics to enhance thermal performance, preventing overheating and extending device longevity.
Thermal gap pads play a crucial role in these applications by providing efficient heat transfer and thermal management solutions. They address problems related to overheating, thermal resistance, and component reliability, ensuring the optimal performance and longevity of electronic and mechanical systems across various industries.
COMPARE
Compare Options
Empower your decision with a tailored comparison chart for the perfect application fit. Compare specifications, brands, and pricing.
1
2
3
1 | 2 | 3 | |
Consideration | Silicone-Based Gap Pads |
Graphite-Based Gap pads |
Phase Change Gap Pads |
Thermal Conductivity | Good | Very Good | Very Good |
Conformability | Very Good | Moderate | Good |
Electrical Insulation | Very Good | Good | Good |
Operating Temperature | Good | Very Good | Good |
Outgassing | Good | Very Good | Good |
Flame Resistance | Moderate | Good | Moderate |
Durability | Good | Very Good | Good |
Customization Options | Very Good | Good | Moderate |
Cost-effectiveness | Good | Moderate | Good |
Application Versatility | Very Good | Moderate | Good |