Product Description
Matrix EMI Shielding Vents are engineered solutions designed to mitigate electromagnetic interference (EMI) in electronic enclosures. These vents offer superior EMI shielding effectiveness, typically exceeding 60dB from 200 MHz to 10 GHz, ensuring robust performance. Engineers benefit from their lightweight, corrosion-resistant construction, promoting design flexibility and durability. Widely adopted in telecommunications, automotive, and aerospace applications, Matrix EMI Shielding Vents safeguard sensitive electronics by maintaining optimal EMI protection while allowing for proper ventilation, enhancing overall system reliability.
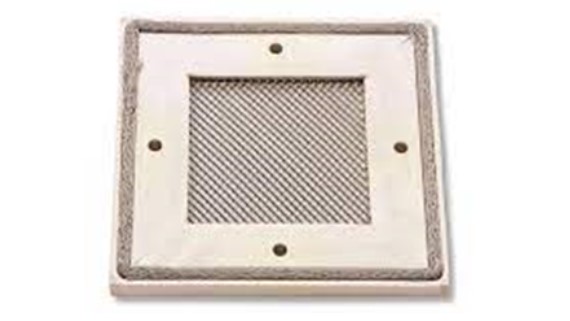
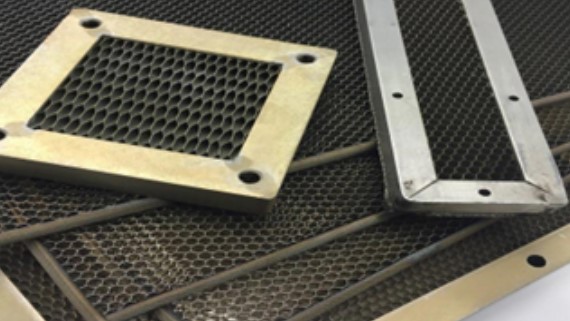
Value Added
Matrix adds value in-house by tailoring EMI vents to specific applications. We can employ techniques like finite element analysis (FEA) to optimize vent geometry, ensuring maximum shielding effectiveness. Material selection via impedance matching enhances attenuation, addressing unique frequency requirements.
Frequently asked questions
If you have a question that is not addressed in our FAQ please click 'Contact Matrix' at the top of the page and submit. We will answer directly and add it to our FAQ to benefit the entire engineering community.
Your vision! Our expertise! Collaborating with engineering teams is what we do best! We listens to your priorities, and create a customized solution tailored to your specific requirements.
1. Honeycomb Vents
- Description: Hexagonal cell structure composed of conductive materials.
- Benefit: High shielding effectiveness due to multiple reflection paths within the honeycomb, ideal for EMI-sensitive applications.
2. Vent Panels with Gaskets
- Description: Metal or conductive plastic panels with integrated gaskets.
- Benefit: Provides EMI protection while also sealing against environmental factors, suitable for harsh environments.
3. Wire Mesh Vents
- Description: Fine metal or conductive wire mesh construction.
- Benefit: Allows for effective EMI shielding while permitting airflow and maintaining visibility in applications like displays.
4. Fingerstock Gaskets
- Description: Elastomeric gaskets with conductive metal fingers.
- Benefit: Excellent EMI sealing and flexibility, conforming to irregular surfaces and complex enclosures.
5. EMI Vent Materials (e.g., Foam and Fabric)
- Description: Electrically conductive foams or fabrics.
- Benefit: Flexible and lightweight materials ideal for custom EMI solutions and conformal applications.
6. Die-Cast Vents
- Description: EMI vents constructed through die-casting techniques.
- Benefit: Durable and rigid construction, often used in rugged environments and aerospace applications.
7. Specialty Materials (e.g., Mu-metal)
- Description: Unique alloys with exceptional magnetic shielding properties.
- Benefit: Highly effective at blocking low-frequency magnetic fields, crucial in MRI and scientific instruments.
8. Micro-Perforated Vents
- Description: Fine micro-perforations on a metal sheet.
- Benefit: Offers high airflow while still providing EMI shielding for applications with strict thermal requirements.
9. Thermoplastic EMI Vents
- Description: EMI vents made from conductive thermoplastic materials.
- Benefit: Lightweight, cost-effective, and suitable for various applications requiring moderate EMI protection.
10. Hybrid EMI Vents
- Description: Combines multiple materials or structures to optimize shielding effectiveness.
- Benefit: Tailored solutions for complex EMI challenges, ensuring maximum performance.
11. Waveguide Vents
- Description: Resonant structures designed for specific frequency bands.
- Benefit: Highly specialized EMI vents for precise frequency attenuation, common in microwave and radar applications.
Matrix can leverage these EMI vents and materials to address specific electromagnetic interference challenges in their designs, ensuring the highest level of EMI protection and system reliability.
Conductivity: The foil’s electrical conductivity is crucial. It should be highly conductive to provide effective EMI shielding and grounding.
Thickness: Foil tape thickness affects its durability and conformability. Thicker foils offer better durability but may be less flexible.
Adhesive Type: The adhesive should adhere well to the substrate and maintain its properties over the expected temperature and environmental conditions. Options include acrylic, silicone, or conductive adhesives.
Adhesion Strength: Consider the required bond strength to ensure the tape remains securely attached to the surface over time, especially in high-vibration or high-temperature environments.
Temperature Range: Foil tapes should operate within the required temperature range. Ensure the selected tape can withstand both high and low temperatures without degrading.
Corrosion Resistance: If the application involves exposure to corrosive elements, select a foil tape material that is corrosion-resistant to maintain its shielding properties.
Flexibility: Depending on the application, the tape may need to conform to irregular surfaces. Engineers should choose a tape that offers the necessary flexibility without compromising shielding effectiveness.
Shielding Effectiveness: Evaluate the foil tape’s shielding effectiveness against the specific frequencies and electromagnetic interference levels relevant to the application. This may involve testing or using materials with known shielding performance.
Durability: Consider the expected service life and environmental conditions, such as exposure to UV radiation or chemicals, to ensure the tape’s long-term reliability.
Tape Width and Length: Select the appropriate tape width and length to match the application’s requirements and reduce waste.
Compliance: Ensure that the selected foil tape material complies with relevant industry standards and regulations, especially if it is used in applications where EMI shielding is critical, such as aerospace or medical devices.
Cost: Balance the technical requirements with budget constraints, considering the overall cost-effectiveness of the chosen foil tape.
Installation and Removal: Evaluate ease of installation and removal, as well as any residue left behind after removal, which can impact maintenance and rework processes.
Environmental Impact: Consider the environmental impact of the tape material, including factors like recyclability and disposal requirements.
EMI (Electromagnetic Interference) vents find common use in various applications across industries to address specific electromagnetic interference problems. Here are some technical examples:
1. Military Aircraft Avionics
- Problem: Electromagnetic interference can disrupt critical avionics systems in military aircraft.
- Solution: EMI vents are employed to allow for pressure equalization while blocking external electromagnetic interference, ensuring the reliable operation of avionics.
- Application: F-35 Lightning II fighter jets use EMI vents in their avionics systems.
2. Telecommunications Base Stations
- Problem: EMI can degrade the performance of sensitive RF components in base station equipment.
- Solution: EMI vents provide EMI shielding, allowing for proper ventilation to prevent overheating and signal degradation.
- Application: EMI vents are utilized in 5G base station enclosures to maintain signal quality.
3. Medical Imaging Devices (MRI)
- Problem: Electromagnetic interference can introduce artifacts and reduce image quality in MRI scans.
- Solution: EMI vents are incorporated into MRI shielding to maintain RF shielding while enabling ventilation, ensuring high-quality diagnostic imaging.
- Application: Siemens MAGNETOM MRI machines feature EMI vents in their shielding designs.
4. Industrial Automation Enclosures
- Problem: EMI can disrupt sensitive automation equipment and sensors in manufacturing environments.
- Solution: EMI vents facilitate cooling and EMI protection, ensuring reliable operation of automation systems.
- Application: Enclosures housing PLCs (Programmable Logic Controllers) in manufacturing facilities use EMI vents.
5. Consumer Electronics
- Problem: Electronic devices emit EMI that can interfere with other nearby devices.
- Solution: EMI vents in consumer electronics help reduce emissions and maintain device compliance with regulatory standards.
- Application: EMI vents are found in smartphones, tablets, and laptops.
6. Aerospace Radomes
- Problem: EMI can affect radar and communication systems in aircraft.
- Solution: Radome EMI vents enable radar signals to pass through while attenuating external interference.
- Application: Commercial and military aircraft employ EMI vents in their radomes.
7. Automotive Electronic Control Units (ECUs)
- Problem: Automotive ECUs are sensitive to EMI, affecting vehicle performance.
- Solution: EMI vents shield ECUs from interference while allowing for airflow to prevent overheating.
- Application: Automotive manufacturers integrate EMI vents into ECU enclosures.
8. Data Centers
- Problem: EMI can disrupt data center servers and networking equipment.
- Solution: EMI vents in server racks and enclosures maintain electromagnetic compatibility while supporting efficient cooling.
- Application: Large-scale data centers deploy EMI vents in their infrastructure.
In each of these applications and industries, EMI vents serve as a technical solution to the specific problem of electromagnetic interference. They allow for proper ventilation, heat dissipation, and protection of sensitive electronics, ensuring the reliability and performance of critical systems and devices.
COMPARE
Compare Options
Click below to get a customized comparison chart tailored to your application.
1
2
3
1 | 2 | 3 | |
Consideration | Honeycomb Vents |
Vent Panels with Gaskets |
Wire Mesh Vents |
Conductivity | Very Good | Good | Good |
Thickness | Good | Moderate | Good |
Adhesive Type | Good | Good | Good |
Adhesion Strength | Good | Very Good | Good |
Temperature Range | Very Good | Good | Good |
Corrosion Resistance | Good | Very Good | Moderate |
Flexibility | Moderate | Good | Very Good |
Shielding Effectiveness | Very Good | Good | Good |
Durability | Good | Very Good | Good |
Installation and Removal | Good | Good | Good |