Product Description
Matrix High-Reliability (Hi-Rel) connectors encompass a diverse range, including hermetic, rugged, and EMC-compliant variants, to ensure unmatched performance in demanding environments. Engineers benefit from their exceptional durability, sealing, and electromagnetic compatibility features, making them indispensable in industries such as aerospace, defense, medical, and oil and gas. These connectors deliver robust connectivity solutions, with precision and resilience to extreme conditions, meeting stringent standards for mission-critical applications.
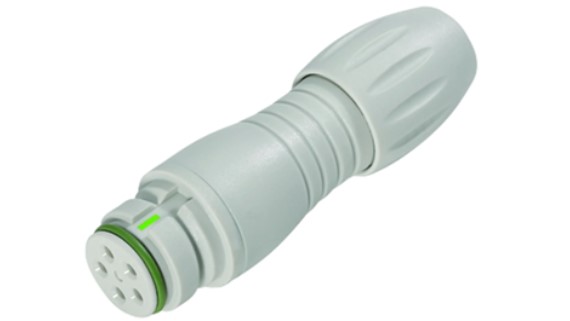
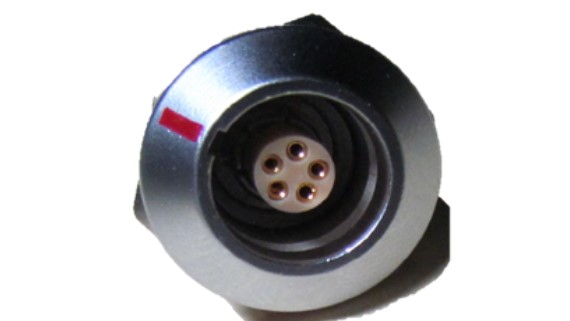
Value Added
Matrix adds significant value for engineering teams by customizing high-reliability connectors into tailored harnesses and assemblies. Our expertise in overmolding, connector gaskets, and ruggedized cables ensures superior reliability, EMI protection, and environmental resilience. Customized assemblies reduce complexity, minimize failure points, and optimize cable management, streamlining integration and simplifying the engineering process for demanding applications.
Frequently asked questions
If you have a question that is not addressed in our FAQ please click 'Contact Matrix' at the top of the page and submit. We will answer directly and add it to our FAQ to benefit the entire engineering community.
Your vision! Our expertise! Collaborating with engineering teams is what we do best! We listens to your priorities, and create a customized solution tailored to your specific requirements.
1. Hermetic Connectors:
- Description: Hermetic connectors provide airtight seals, preventing moisture and contaminants from entering sensitive electronic systems.
- Benefit: Ideal for aerospace and military applications, they ensure long-term reliability in harsh environments. Common standards: MIL-DTL-38999, MIL-DTL-26482.
2. Rugged Connectors:
- Description: Rugged connectors feature robust construction and environmental sealing to withstand extreme conditions.
- Benefit: Vital in industries like oil and gas, they ensure uninterrupted connectivity in harsh, high-vibration, and high-temperature environments. Common standards: MIL-DTL-5015, MIL-DTL-26482.
3. EMC-Compliant Connectors:
- Description: Electromagnetic Compatibility (EMC) compliant connectors minimize interference and emissions, crucial for sensitive electronics.
- Benefit: Ensures reliable signal integrity in critical applications, such as medical devices and telecommunications. Common standards: IEC 60601, EN 55032.
4. Circular Connectors:
- Description: Circular connectors feature a circular interface with multiple pins, suitable for a wide range of applications.
- Benefit: Versatile and reliable, they find use in aviation, military, and industrial settings. Common standards: MIL-DTL-38999, MIL-DTL-5015.
5. Rectangular Connectors:
- Description: Rectangular connectors have a block-like shape, often used in industrial and automotive applications.
- Benefit: Enable high-density connections, facilitating data transmission in robotics and automation. Common standards: MIL-DTL-83513, DIN 41612.
6. Fiber Optic Connectors:
- Description: Fiber optic connectors transmit data using light signals, offering high bandwidth and immunity to electromagnetic interference.
- Benefit: Crucial for high-speed data transmission in telecommunications and data centers. Common standards: MIL-PRF-83526, IEC 61753.
7. Miniature Connectors:
- Description: Miniature connectors are compact, lightweight, and suitable for applications with space constraints.
- Benefit: Enable connectivity in small devices like medical instruments and portable electronics. Common standards: MIL-DTL-32139, M12 connectors.
8. Coaxial Connectors:
- Description: Coaxial connectors provide high-frequency signal transmission, commonly used for RF and microwave applications.
- Benefit: Maintain signal integrity in aerospace, defense, and telecommunications. Common standards: MIL-PRF-39012, IEC 61169.
9. PCB Connectors:
- Description: PCB connectors are designed for easy integration onto printed circuit boards (PCBs).
- Benefit: Streamline PCB design and assembly processes in various industries. Common standards: DIN 41612, MIL-DTL-55302.
10. Custom and Specialty Connectors:
- Description: Custom connectors are engineered to meet unique requirements, offering tailored solutions for specific applications.
- Benefit: Address specific engineering challenges, ensuring compatibility, reliability, and performance in specialized industries.
1. MIL-DTL-38999:
- Circular connectors with a cylindrical shape, multiple pins (contacts), and threaded coupling for robust and secure connections. Known for their durability and versatility, they are used in aerospace and military applications.
2. MIL-DTL-5015:
- Circular connectors with a cylindrical shape, threaded coupling, and multiple pins. These rugged connectors are used in industrial and military applications and are known for their reliability.
3. MIL-DTL-26482:
- Circular connectors with a cylindrical shape, bayonet coupling, and multiple pins. They are environmentally sealed and widely used in aerospace and military applications.
4. IEC 60601:
- Rectangular and circular connectors used in medical equipment. They often have unique pin configurations and insulating materials to ensure safety and reliability in healthcare settings.
5. EN 55032:
- Connectors designed to meet electromagnetic compatibility (EMC) standards, ensuring minimal interference and emissions in multimedia equipment.
6. MIL-DTL-83513:
- Miniature rectangular connectors with a compact shape and multiple pins. They are used in aerospace and military applications where space is limited.
7. DIN 41612:
- Rectangular connectors with a block-like shape, multiple pins, and various configurations. Widely used in industrial and electronics applications.
8. MIL-PRF-83526:
- Fiber optic connectors designed for military and aerospace applications, featuring precision alignment and high-speed data transmission.
9. IEC 61753:
- Standards for fiber optic connector interfaces, including shapes like SC, LC, and MTP/MPO connectors, with various pin counts and configurations.
10. MIL-PRF-32139:
- Miniature connectors with a compact shape, ideal for applications where space is limited, such as in military and aerospace equipment.
11. M12 connectors:
- Circular connectors with a threaded coupling mechanism, available in various pin configurations, commonly used in industrial automation and sensors.
12. MIL-PRF-39012:
- Coaxial connectors for radio-frequency (RF) applications, available in various shapes, such as BNC, N, and SMA connectors.
13. IEC 61169:
- Radio-frequency connectors with unique shapes like 7/16 DIN and QMA, designed for specific RF applications.
14. MIL-DTL-55302:
- Rectangular connectors with a block-like shape and multiple pins, designed for printed circuit board (PCB) applications.
15. MIL-PRF-85045:
- Rectangular connectors for aerospace and military applications, available in various shapes and pin configurations.
16. MIL-PRF-28748:
- Connectors for electronic equipment, featuring rectangular and circular shapes with multiple pins.
17. MIL-PRF-55110:
- Connectors and sockets designed for printed wiring boards, ensuring reliable connections in electronic systems.
18. IEC 60320:
- Standards for connectors used in household and similar electrical appliances, featuring various shapes like C13, C14, and C15 connectors.
19. USB Type-C:
- Universal Serial Bus (USB) connectors with a reversible, compact shape, offering high-speed data transfer and power delivery.
20. RJ45 connectors:
- Rectangular connectors with eight pins, commonly used in Ethernet networking applications.
21. RJ11 connectors:
- Rectangular connectors with four to six pins, used for telephone and data communication in homes and offices.
22. D-subminiature connectors:
- Rectangular connectors with a distinctive D-shaped shell and multiple pins, available in various sizes and pin configurations.
23. MIL-DTL-83513:
- Micro-D connectors with a compact rectangular shape, ideal for aerospace and military applications with limited space.
24. MIL-DTL-83527:
- Nano-D connectors, even smaller than Micro-D connectors, suitable for ultra-miniaturized applications in aerospace and defense.
25. MIL-DTL-32139:
- Nano miniature connectors, offering a balance between size and functionality for demanding aerospace and military applications.
26. IEC 60130:
- Round connectors with threaded coupling, used in audio and video equipment for robust connections.
27. MIL-DTL-28748:
- Circular connectors with a rugged design, suitable for harsh environments and military applications.
28. MIL-PRF-39012:
- Coaxial connectors, including types like SMA, N, and BNC connectors, used in RF and microwave applications.
29. IEC 61984:
- Rectangular connectors with a wide range of configurations and pin counts, used in industrial automation and machinery.
30. IEC 61076:
- Rectangular connectors with specific shapes and pin configurations, designed for industrial and telecommunications applications.
31. DIN 43650:
- Rectangular connectors with a specific shape and pin configuration, commonly used in solenoid valve applications.
32. MIL-DTL-55302:
- Rectangular connectors with a block-like shape, available in various sizes and pin configurations, designed for PCB applications.
33. MIL-PRF-83522:
- Circular connectors designed for aerospace and military applications, available in various sizes and configurations.
34. IEC 60947:
- Rectangular connectors used in low-voltage switchgear and control gear applications, ensuring reliable electrical connections.
35. MIL-DTL-83723:
- Circular connectors designed for military and aerospace applications, featuring a robust and versatile design.
36. MIL-DTL-24643:
- Connectors used in shipboard electrical and electronic systems, ensuring reliable performance in maritime environments.
37. MIL-DTL-83526:
- Fiber optic connectors with a rugged design for military and aerospace applications, offering high-speed data transmission.
38. IEC 61076:
- Rectangular connectors with a specific shape and pin configuration, commonly used in industrial automation and robotics.
39. MIL-PRF-21038:
- Connectors used in missile and ordnance systems, ensuring reliability and performance in demanding military applications.
40. MIL-PRF-6106:
- Circular connectors designed for use in aircraft electrical systems, offering reliable connections in aerospace applications.
1. Application Requirements:
- Understand the specific requirements of your application, such as signal type (analog, digital, RF), power requirements, data rates, and environmental conditions (temperature, humidity, pressure, vibration, shock).
2. Environmental Conditions:
- Consider the operating environment, including temperature extremes, exposure to chemicals, radiation, or other harsh conditions. Choose a connector that can withstand these conditions.
3. Durability and Reliability:
- High-rel connectors should be designed for long-term reliability. Consider factors such as contact cycle life, wear resistance, and resistance to oxidation or corrosion.
4. Size and Form Factor:
- Ensure that the connector’s size and form factor fit within the available space in your design. Miniaturization may be important in some applications.
5. Electrical Performance:
- Evaluate the connector’s electrical characteristics, such as impedance matching, signal integrity, and crosstalk. Ensure that it meets your performance requirements.
6. Mechanical Design:
- Examine the connector’s mechanical features, including mating and unmating forces, retention mechanisms, and ease of installation. It should be robust and easy to work with.
7. Mating and Unmating Cycles:
- High-rel connectors are often required to withstand a large number of mating and unmating cycles. Ensure the connector is rated for the expected number of cycles in your application.
8. Connector Materials:
- The choice of materials can impact the connector’s performance and durability. Consider factors like material compatibility with your application and resistance to environmental factors.
9. Hermetic Sealing:
- In applications where preventing moisture, dust, or gases from entering the connector is crucial, consider connectors with hermetic sealing options.
10. EMI/RFI Shielding:
- If your application is sensitive to electromagnetic interference (EMI) or radio-frequency interference (RFI), select connectors with effective shielding features.
11. Connector Compatibility:
- Ensure that the chosen connector is compatible with the cables and PCBs used in your system. Compatibility issues can lead to problems during assembly and operation.
12. Standards and Certifications:
- Look for connectors that meet industry standards and certifications, especially in highly regulated industries like aerospace and medical. Examples include MIL-STD, IPC, or ISO standards.
13. Cost Considerations:
- While quality and reliability are paramount, cost is also a factor to consider. Balance the cost of the connector with its performance and reliability benefits.
14. Supplier and Support:
- Evaluate the reputation and track record of the connector manufacturer. Consider the availability of technical support and after-sales service.
15. Documentation and Traceability:
- Ensure that the connector comes with proper documentation, including datasheets, drawings, and traceability information, which can be essential for quality control and maintenance.
16. Future Availability:
- High-rel connectors often have long lifecycles. Consider the long-term availability of the connector to avoid obsolescence issues.
17. Testing and Qualification:
- Consider conducting rigorous testing and qualification procedures to ensure that the chosen connector meets your application’s requirements and standards.
1. Space Exploration:
- Problem: In space missions, connectors must withstand extreme temperatures, radiation, and vacuum conditions while ensuring reliable data transmission.
- Solution: High-rel connectors with radiation-hardened materials and hermetic sealing ensure robust communication in spacecraft.
- Reference: NASA’s Mars rovers, such as Perseverance, use high-reliability connectors for mission-critical systems.
2. Medical Implantable Devices:
- Problem: Implantable medical devices require connectors that can endure body fluids, maintain electrical connections, and minimize tissue response.
- Solution: High-rel connectors with biocompatible materials and insulation minimize the risk of infections and ensure long-term reliability in devices like pacemakers.
- Reference: Medtronic’s implantable medical devices incorporate high-reliability connectors.
3. Submarine Communication Systems:
- Problem: Submarine communication systems need connectors that can operate underwater at extreme pressures while maintaining data integrity.
- Solution: High-rel connectors designed for subsea applications provide reliable signal transmission and sealing against water ingress.
- Reference: Navies worldwide employ high-reliability connectors in their submarine communication systems.
4. High-Speed Data Centers:
- Problem: Data centers require connectors that can handle high data rates, minimize signal loss, and maintain data integrity in server racks.
- Solution: High-rel connectors designed for high-speed data transmission ensure low latency and data center efficiency.
- Reference: Companies like Amazon Web Services (AWS) use high-reliability connectors in their data centers.
5. Railway Signaling and Control:
- Problem: Railway signaling systems need connectors that can endure harsh weather conditions, vibrations, and ensure reliable communication for train control.
- Solution: High-rel connectors with rugged designs and resistance to temperature variations support safe and efficient railway operations.
- Reference: Leading rail companies like Siemens rely on high-reliability connectors in their signaling systems.
6. Satellite Communication:
- Problem: Satellite communication systems demand connectors that can operate in the vacuum of space, handle high-frequency signals, and resist radiation.
- Solution: High-rel connectors with space-rated materials and shielding enable reliable data transmission between satellites and ground stations.
- Reference: Satellite operators like SpaceX use high-reliability connectors for their satellite constellations.
7. Automated Industrial Machinery:
- Problem: Industrial automation equipment requires connectors that can withstand continuous operation, vibrations, and ensure robust data and power connections.
- Solution: High-rel connectors with industrial-grade durability support the reliable operation of manufacturing machinery.
- Reference: Manufacturing companies like Bosch use high-reliability connectors in their production lines.
8. Underwater Robotics:
- Problem: Underwater robots (ROVs) require connectors that can operate at extreme depths, maintain signal integrity, and resist corrosion.
- Solution: High-rel connectors designed for subsea applications support data transmission and power supply in underwater exploration.
- Reference: Oceanographic research institutions use high-reliability connectors in their ROVs.
9. Renewable Energy Systems:
- Problem: Renewable energy installations, such as wind turbines and solar farms, need connectors that can endure outdoor exposure, temperature variations, and ensure efficient power transmission.
- Solution: High-rel connectors with weatherproofing and high current-carrying capacity support the reliability of renewable energy systems.
- Reference: Renewable energy companies like Vestas use high-reliability connectors in their wind turbines.
10. Unmanned Aerial Vehicles (UAVs):
- Problem: UAVs require connectors that can withstand flight vibrations, temperature fluctuations, and ensure secure connections for data links and sensors.
- Solution: High-rel connectors with lightweight and robust designs support reliable communication and control in UAVs.
- Reference: UAV manufacturers like DJI incorporate high-reliability connectors in their drone platforms.
These examples illustrate the wide range of industries and applications where high-reliability connectors play a crucial role in addressing specific technical challenges related to reliability, durability, and performance.
COMPARE
Compare Options
Click below to get a customized comparison chart tailored to your application.
1
2
3
1 | 2 | 3 | |
Considerations | Type A Connector | Type B Connector | Type C Connector |
Application Requirements | Very Good | Good | Good |
Environmental Conditions | Very Good | Good | Moderate |
Durability and Reliability | Very Good | Good | Moderate |
Size and Form Factor | Good | Very Good | Moderate |
Electrical Performance | Very Good | Good | Good |
Mechanical Design | Good | Very Good | Moderate |
Mating and Unmating Cycles | Very Good | Good | Moderate |
Connector Materials | Good | Very Good | Moderate |
Hermetic Sealing | Moderate | Very Good | Good |
EMI/RFI Shielding | Very Good | Good | Good |